pp twin wall sheet making machine
Date:2020/4/24 10:05:17 / Read: / Source:This website
A pp twin wall sheet making machine is used to produce corrugated plastic sheets with two outer flat layers and an inner corrugated layer. These sheets are commonly used for signage, packaging, and construction applications.
What is the process and operating flow of the pp twin wall sheet making machine?
The process and operating flow of a polypropylene (PP) twin wall sheet making machine is as follows:
1. Plastic Pellet Feeding:
- Polypropylene plastic pellets are loaded into the hopper of the extruder.
2. Melting and Extrusion:
- The extruder heats and melts the PP pellets into a viscous, molten state.
- The molten plastic is then forced through a specially designed die that gives it the twin wall profile.
3. Sheet Forming:
- As the molten PP sheet exits the die, it passes through a series of rollers that shape and cool the sheet.
- These rollers help create the distinct corrugated interior structure between the two flat outer layers.
4. Cooling:
- After passing through the forming rollers, the PP twin wall sheet is cooled, typically using a combination of ambient air and/or chilled rollers.
- Proper cooling is crucial to set the sheet's structure and dimensions.
5. Cutting and Stacking:
- Once cooled, the continuous PP twin wall sheet is cut to the desired length using a rotating blade or shear.
- The cut sheets are then automatically stacked for packaging and shipping.
6. Winding (optional):
- Alternatively, the continuous PP twin wall sheet can be wound onto a take-up reel for later cutting and stacking.
The entire process is typically automated and computer-controlled to ensure consistent quality and production rates. Key parameters like melt temperature, roller speeds, and cutting intervals are all carefully monitored and adjusted as needed.
PP multi-wall sheet machine
Sheet thickness(mm) |
Weight(g/㎡) |
Line speed(m/min) |
2 |
300-550 |
4-8 |
3 |
400-650 |
3-6 |
4 |
550-850 |
2-5 |
5 |
650-950 |
1-4 |
6 |
750-1100 |
1-3 |
Main Parts of pp twin wall sheet making machine
1.Single screw extruder
2.Hydraulic
pressure quick change filter net
3.Die
4.Calibration
table
5.First
haul-off unit
6. Oven
7.Cooling
station
8.Second
haul-off unit
9.Cutting
unit
10.Automatic
control cabinet
11.Stack table
12.Screw loader
Process Flow of pp twin wall sheet making machine
Feeding→extrusion→exchange screen→Die→Calibrator→first haul off →heat treating oven →Cooling→second haul off →cutting→stacking
Benefits of PP hollow profile sheet extrusion machine
1. Required high production efficiency
2. Production flexibility( controllable sheet thickness and width, for example, you can produce 2-6mm thick sheet with the same mould or machine)
3. Reliability and stability
4.Excellent Adaptability to different raw material and reach over 30% production cost reduction.
5. Size and shape diversity of finished products
Applications of pp twin wall sheet making machine
Plastic hollow board, Plastic fluted sheet, Antistatic plastic corrugated sheet, Plastic hollow sheet for electrics bottom protection, PP hollow sheet clapboard, PE hollow board, Plastic advertising display board, Plastic corrugated sheet for bottles layer pallet, PP coroplast sheet, PP carton plast sheet, PP correx sheet, Edge sealing PP corrugated board, PP turnover container box for packaging, PP corrugated packaging box for vegetable export, PP turnover packaging box for asparagus, PP collapsible packaging box for grape, Plastic fire-retarding packaging box, PP packaging box for pesticide, PP hollow sheet backboard for refrigerator and other PP hollow sheet products.
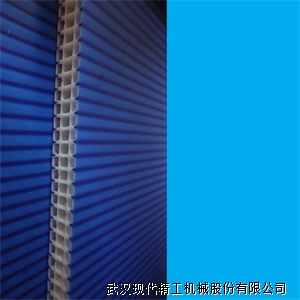
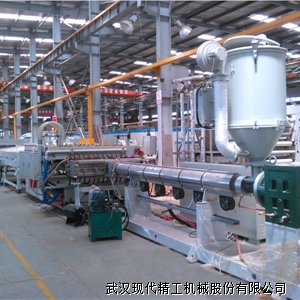
Author:admin