What are the application differences between plastic hollow board and plastic solid board
DATE:2025/1/9 10:32:24 / READ: / SOURCE:This station
Plastic hollow board and plastic solid board are two common types of plastic materials. Although their raw materials are similar, they have significant differences in their application fields due to differences in structure and performance. The main application differences between these two materials are as follows:
1. Structure and Performance
Plastic hollow board: usually made of polypropylene (PP) or polyethylene (PE), with a hollow structure inside, this design makes the hollow board lighter and has good strength and rigidity. Due to the presence of hollow structures, hollow boards have good sound insulation and thermal insulation effects, and can reduce material usage to a certain extent in terms of load-bearing capacity.
Plastic solid board: also produced from materials such as polypropylene or polyethylene, but its structure is solid, meaning it is heavier and stronger than hollow boards at the same thickness. Solid boards have good impact resistance and compressive performance, making them suitable for higher strength requirements.
2. Application Fields
Application of plastic hollow board:
Packaging industry: Hollow boards are widely used for packaging and transportation due to their lightweight and high strength, which can effectively protect items and reduce the risk of damage. It can also be used to manufacture partition boards, such as separating inside boxes and pallets.
Advertising promotion: The surface of the hollow board is easy to print and lightweight, suitable for outdoor and indoor billboards, display boards, and exhibition supplies.
Industrial production: Hollow boards can be used to make baffles, partitions, and temporary components, and their economy and practicality make them popular in the industrial field.
Application of solid plastic board:
Construction industry: Due to its solidity, solid panels are commonly used in construction, decoration, and as substrates, such as making walls, ceilings, and soundproofing panels, providing better support and durability.
Furniture manufacturing: Solid boards have excellent wear resistance and strength, suitable for making furniture such as tabletops, cabinet doors, etc., commonly found in office and home environments.
Transportation facilities: Safety facilities such as traffic signs and roadblocks are usually made of solid board materials to cope with harsh environments and long-term usage needs.
3. Cost considerations
Production cost and sales price: Generally speaking, the production cost of plastic hollow boards is relatively low, so they are more economical in the market and suitable for large-scale applications. In contrast, solid boards usually have higher costs and prices due to differences in raw material usage and manufacturing processes. This also affects their choices, especially when the budget is limited.
4. Weight and portability
Hollow board: Due to its lightweight nature, it is suitable for applications that require frequent movement and transportation, such as temporary events, exhibition displays, etc.
Solid board: Although relatively heavy, this weight brings higher stability and is suitable for situations that require fixed installation or long-term use, such as internal structures of buildings.
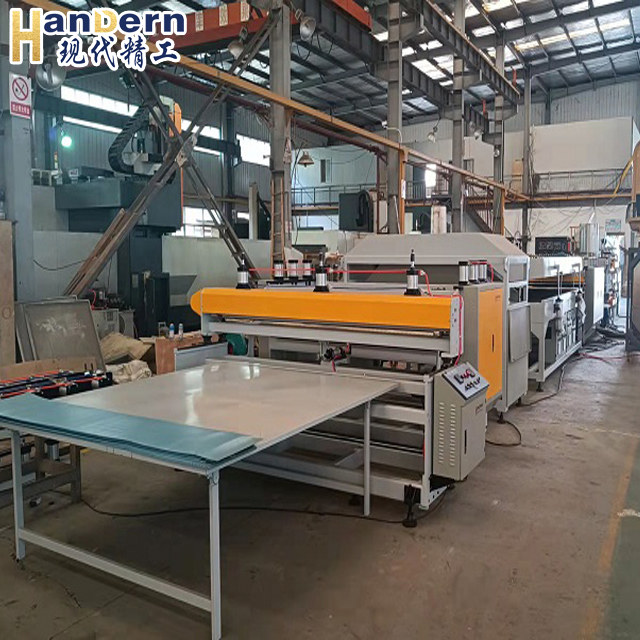
Plastic hollow board: usually made of polypropylene (PP) or polyethylene (PE), with a hollow structure inside, this design makes the hollow board lighter and has good strength and rigidity. Due to the presence of hollow structures, hollow boards have good sound insulation and thermal insulation effects, and can reduce material usage to a certain extent in terms of load-bearing capacity.
Plastic solid board: also produced from materials such as polypropylene or polyethylene, but its structure is solid, meaning it is heavier and stronger than hollow boards at the same thickness. Solid boards have good impact resistance and compressive performance, making them suitable for higher strength requirements.
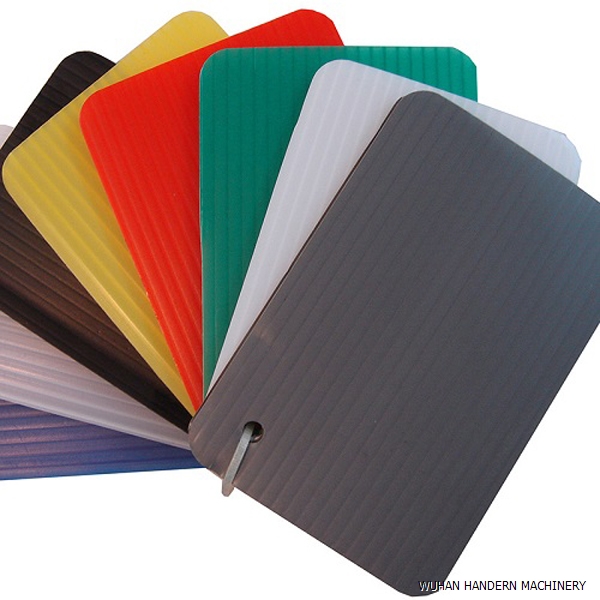
Application of plastic hollow board:
Packaging industry: Hollow boards are widely used for packaging and transportation due to their lightweight and high strength, which can effectively protect items and reduce the risk of damage. It can also be used to manufacture partition boards, such as separating inside boxes and pallets.
Advertising promotion: The surface of the hollow board is easy to print and lightweight, suitable for outdoor and indoor billboards, display boards, and exhibition supplies.
Industrial production: Hollow boards can be used to make baffles, partitions, and temporary components, and their economy and practicality make them popular in the industrial field.
Application of solid plastic board:
Construction industry: Due to its solidity, solid panels are commonly used in construction, decoration, and as substrates, such as making walls, ceilings, and soundproofing panels, providing better support and durability.
Furniture manufacturing: Solid boards have excellent wear resistance and strength, suitable for making furniture such as tabletops, cabinet doors, etc., commonly found in office and home environments.
Transportation facilities: Safety facilities such as traffic signs and roadblocks are usually made of solid board materials to cope with harsh environments and long-term usage needs.

Production cost and sales price: Generally speaking, the production cost of plastic hollow boards is relatively low, so they are more economical in the market and suitable for large-scale applications. In contrast, solid boards usually have higher costs and prices due to differences in raw material usage and manufacturing processes. This also affects their choices, especially when the budget is limited.
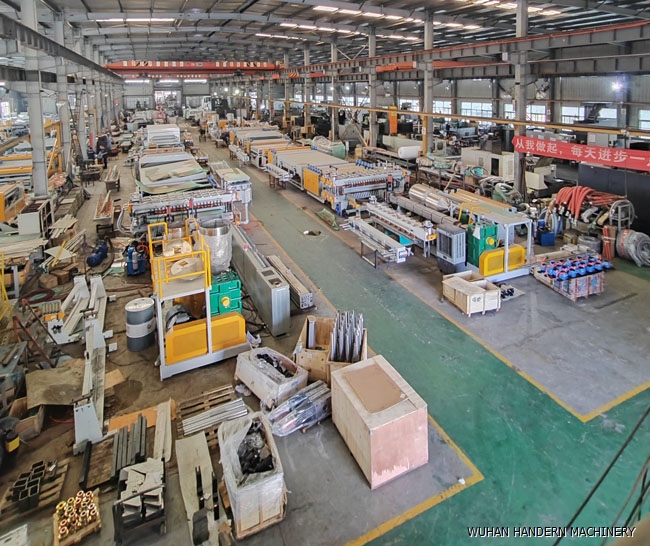
Hollow board: Due to its lightweight nature, it is suitable for applications that require frequent movement and transportation, such as temporary events, exhibition displays, etc.
Solid board: Although relatively heavy, this weight brings higher stability and is suitable for situations that require fixed installation or long-term use, such as internal structures of buildings.
Author:admin