What is the difference between PP and PC hollow board production equipment
DATE:2025/1/10 9:58:37 / READ: / SOURCE:This station
PP (polypropylene) and PC (polycarbonate) hollow boards are two different types of plastic hollow boards, each with its own characteristics, widely used in industries such as packaging, construction, advertising, and transportation. Although they share many similarities in functionality and usage, there are significant differences in their production equipment.
1. Characteristics of raw materials
The difference in physical and chemical properties between PP and PC directly affects the design and operation of production equipment. PP is a relatively lightweight and corrosion-resistant thermoplastic with good formability and flowability, suitable for use in ordinary extrusion molding equipment. PC is a high-strength, high transparency material with better temperature resistance and impact resistance, so its processing requires higher control of temperature and pressure.
2. Production process
The production of PP hollow boards mainly involves three steps: extrusion, molding, and cooling. PP resin is extruded through an extruder, heated and plasticized, and then formed into a hollow structure through a mold, followed by cooling and molding. The production of PC hollow boards requires higher temperature conditions, usually using twin-screw extruders to ensure the uniformity and fluidity of resin mixing. This different process arrangement means that the equipment made of the two materials also differs in structure and components.
3. Extrusion equipment
In terms of extrusion equipment, the production equipment for PP hollow boards is generally equipped with a single screw extruder, while the production of PC hollow boards may require the use of a twin-screw extruder. Twin screw extruder has better mixing effect and plasticizing performance of materials, suitable for PC materials with higher viscosity. In addition, the production equipment for PC hollow boards is usually equipped with a specialized temperature control system to control the temperature of the material during extrusion and prevent material degradation.
4. Mold design
There are also differences in mold design between PP and PC hollow boards. PP hollow board molds are usually designed with simplicity and are suitable for rapid production of large quantities of products; The mold design for PC hollow boards needs to consider higher temperatures and pressures, often using more complex designs to ensure uniform thickness and strength. In addition, the mold for PC hollow boards also needs to use materials that are resistant to high temperatures and corrosion to better adapt to the high temperature environment during the production process.
5. Cooling system
In terms of cooling system, the production of PP hollow boards usually uses water or air cooling systems, which helps with rapid prototyping of products and improves production efficiency. PC hollow boards typically require a more sophisticated cooling system to prevent warping or deformation after molding, which typically requires more precise cooling temperatures and uniform cooling rates.
6. Automation control
Modern PP and PC hollow board production lines are committed to achieving automation, but PC hollow board production lines typically integrate higher end control systems to monitor material flow, temperature, pressure, and cooling processes to ensure high-quality stability of products.
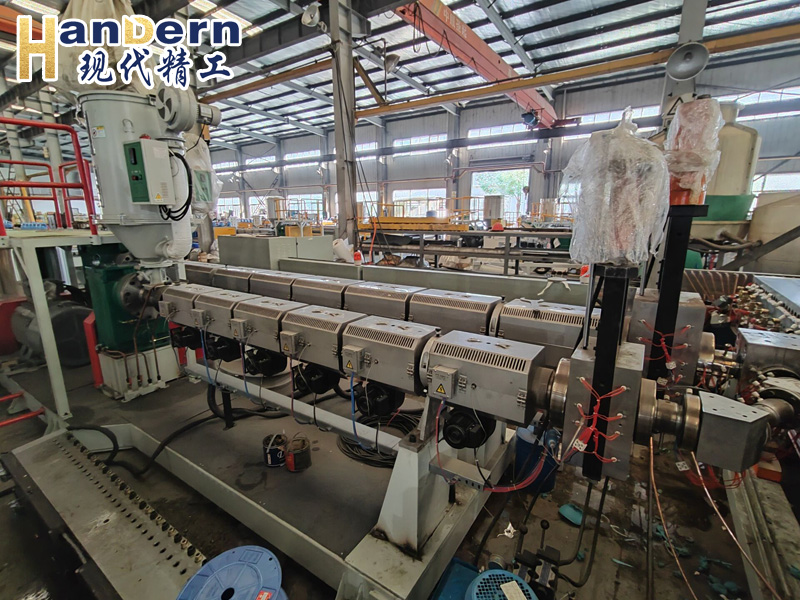
The difference in physical and chemical properties between PP and PC directly affects the design and operation of production equipment. PP is a relatively lightweight and corrosion-resistant thermoplastic with good formability and flowability, suitable for use in ordinary extrusion molding equipment. PC is a high-strength, high transparency material with better temperature resistance and impact resistance, so its processing requires higher control of temperature and pressure.
2. Production process
The production of PP hollow boards mainly involves three steps: extrusion, molding, and cooling. PP resin is extruded through an extruder, heated and plasticized, and then formed into a hollow structure through a mold, followed by cooling and molding. The production of PC hollow boards requires higher temperature conditions, usually using twin-screw extruders to ensure the uniformity and fluidity of resin mixing. This different process arrangement means that the equipment made of the two materials also differs in structure and components.
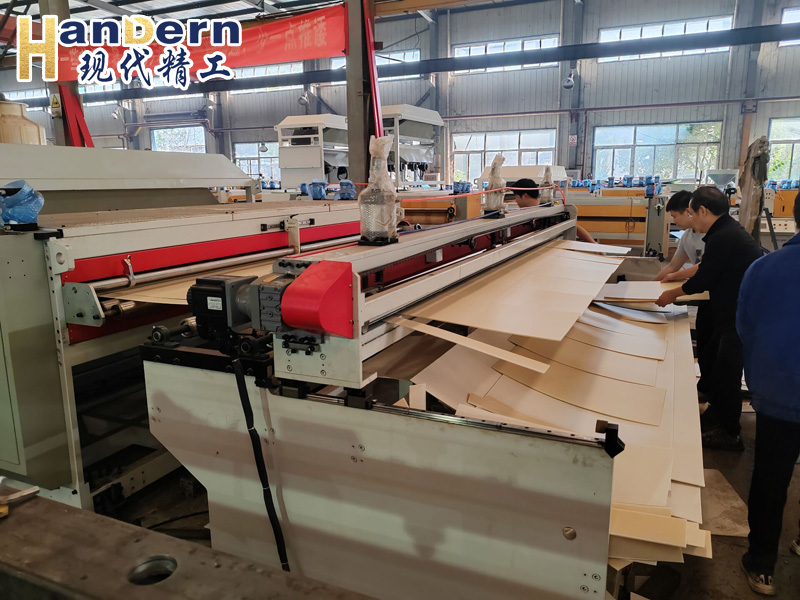
In terms of extrusion equipment, the production equipment for PP hollow boards is generally equipped with a single screw extruder, while the production of PC hollow boards may require the use of a twin-screw extruder. Twin screw extruder has better mixing effect and plasticizing performance of materials, suitable for PC materials with higher viscosity. In addition, the production equipment for PC hollow boards is usually equipped with a specialized temperature control system to control the temperature of the material during extrusion and prevent material degradation.
4. Mold design
There are also differences in mold design between PP and PC hollow boards. PP hollow board molds are usually designed with simplicity and are suitable for rapid production of large quantities of products; The mold design for PC hollow boards needs to consider higher temperatures and pressures, often using more complex designs to ensure uniform thickness and strength. In addition, the mold for PC hollow boards also needs to use materials that are resistant to high temperatures and corrosion to better adapt to the high temperature environment during the production process.
5. Cooling system
In terms of cooling system, the production of PP hollow boards usually uses water or air cooling systems, which helps with rapid prototyping of products and improves production efficiency. PC hollow boards typically require a more sophisticated cooling system to prevent warping or deformation after molding, which typically requires more precise cooling temperatures and uniform cooling rates.

Modern PP and PC hollow board production lines are committed to achieving automation, but PC hollow board production lines typically integrate higher end control systems to monitor material flow, temperature, pressure, and cooling processes to ensure high-quality stability of products.
There are significant differences in the production equipment of PP and PC hollow boards in terms of raw material characteristics, production processes, extrusion equipment, mold design, cooling systems, and automation control. These differences stem from the differences in physical and chemical properties between the two. Therefore, when selecting production equipment, enterprises should choose the appropriate equipment type and configuration based on their own production goals and market demand to ensure product quality and production efficiency.
Author:admin