What are the sizes and models of hollow board production machinery used for stone plastic boxes
DATE:2025/1/20 10:35:46 / READ: / SOURCE:This station
There are various sizes and models of mechanical equipment used in the production process of hollow boards for stone plastic boxes, and their selection mainly depends on factors such as the specifications, production capacity, and process requirements of the final product. The following are some common sizes, models, and characteristics of stone plastic hollow board production machinery.
The twin-screw extruder is the core equipment for the production of stone plastic hollow boards, and the difference in screw diameter and length determines its production capacity and applicable materials. In the market, common screw sizes include:
Diameter: 45mm-120mm: The smaller 45mm model is suitable for small batch production and flexible material processing, while equipment with a diameter of over 100mm is suitable for producing large-scale hollow boards with higher plasticizing capacity and production efficiency.
Length to diameter ratio (L/D): up to 30:1 or higher: The larger the length to diameter ratio, the better the plasticization and mixing effect of the extruder material, making it suitable for producing high filling stone plastic products. The aspect ratio is generally between 20:1 and 30:1, and can be selected according to production needs.
2. Size and model of the mold system
The mold is a key part that affects the shape and size of the hollow board, and its design is usually based on the specifications of the production line. There are the following choices for mold size:
Width: Adjustable range from 1250mm to 3200mm: The wider the mold, the more suitable it is to produce wider hollow boards in one extrusion, making it suitable for the production of large stone plastic boxes.
Thickness: 2mm to 12mm: Different thicknesses of molds are suitable for hollow boards with different purposes. Generally, in fields such as packaging and construction, 3-6mm molds are chosen.
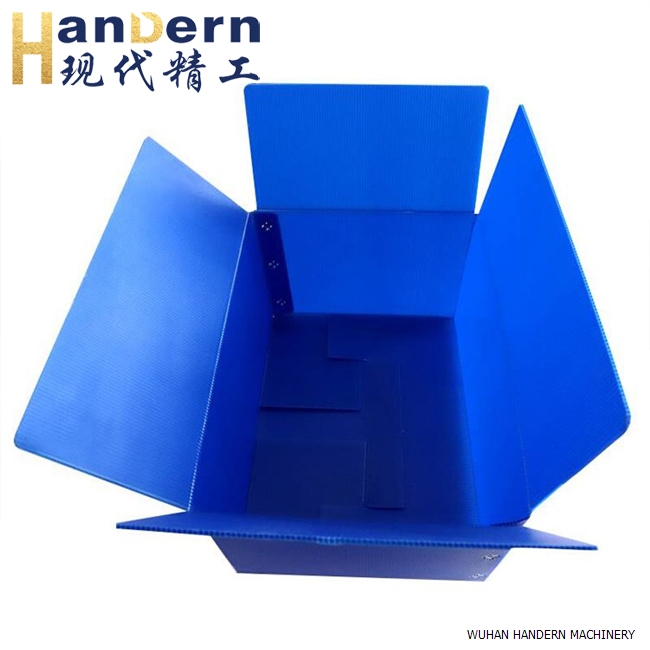
The design of the cooling system also needs to be adapted to the production scale, and common models include:
Cooling trough size: The length is usually between 3 meters and 6 meters, and the width varies from 1 meter to 2 meters, depending on the output of the extruder and the width of the board.
Hose cooling system: The diameter of the pipe is usually 50mm to 100mm, suitable for cooling needs of various formed hollow boards. The design of the cooling system must take into account the flow requirements to ensure rapid cooling and shaping.
4. Size and model of cutting machine
The choice of cutting machine also affects the specifications of the final product, and common sizes include:
Workbench length: 1.5 meters to 5 meters: The length of the workbench determines the maximum length of the board that can be processed. For high production efficiency production lines, it is recommended to use cutting machines with a length of 3 meters or more.
Cutting accuracy: The high-precision cutting machine can control the cutting error within ± 1mm, suitable for stone plastic box products that require strict specifications.
5. Size and model of the control system
Although the control system does not directly affect the physical dimensions of the hollow board, the efficiency and intelligence of its operating interface are crucial in production. Common dimensions include:
Control panel size: generally a touch screen of 10 inches to 20 inches, which facilitates real-time monitoring of production status and parameter adjustment by operators.
Cabinet size: The size of Servo drive and PLC control cabinets is usually 600mm x 800mm x 400mm (width x height x depth), designed according to the number of devices and control requirements.
There are various sizes and models of hollow board production machinery for stone plastic boxes in the market. Among them, the selection of equipment such as twin-screw extruders, molds, cooling systems, cutting machines, and control systems should be reasonably matched according to production needs, production capacity requirements, and final product specifications.
Author:admin