How to deal with emergency stop faults of plastic hollow board pulling machine
DATE:2024/11/21 10:24:39 / READ: / SOURCE:This station
The plastic hollow board pulling machine may experience emergency stop faults during the production process, which not only affect production efficiency but may also have adverse effects on equipment and product quality. When encountering an emergency stop malfunction, operators need to quickly and calmly handle the problem to ensure safety and the normal operation of the equipment. The following are detailed steps and suggestions for dealing with emergency stop faults in plastic hollow board pulling machines.
1. Confirm safety
Before troubleshooting and handling faults, the first thing to ensure is the safety of operators and surrounding staff. Immediately stop other ongoing operations to avoid restarting the device and prevent accidental injury. In addition, the power supply of the relevant equipment should be kept off to ensure that there is no electricity in the operating area.
2. Check the cause of the malfunction
Emergency stop faults may be caused by various reasons, and operators need to conduct item by item inspections:
Emergency stop button: Check if the emergency stop button is pressed incorrectly or stuck. Usually, long pressing this button will cause the device to stop running.
Sensor malfunction: Check if there is a sensor malfunction or alarm. The failure of sensors may cause the equipment to stop running.
Electrical malfunction: Check the electrical system of the equipment, including power supply, cables, and contactors, to see if there are any short circuits or open circuits.
Mechanical failure: Check the mechanical components of the machine, including rollers, chains, and their drive systems, to ensure that they are not stuck or damaged.
3. View the control panel
Search for fault codes and alarm information through the display information on the control panel. Many modern plastic hollow board pulling machines are equipped with displays that can provide detailed information about the reasons for downtime, facilitating troubleshooting.
4. Troubleshooting
After identifying the cause of the malfunction, handle it according to the nature of the problem:
Simple malfunction: If the emergency button is pressed incorrectly, reset the button and restart the device to see if it can operate normally.
Replace faulty parts: If sensors or electrical components are found to be damaged, the corresponding parts should be replaced in a timely manner and necessary debugging should be carried out.
Mechanical inspection and lubrication: If the shutdown is caused by mechanical jamming, it is necessary to manually inspect and clean the jamming material, and lubricate if necessary.
5. Restart the device
After resolving the malfunction, ensure that all safety measures are in place, ensure that the equipment is functioning properly, and conduct inspections to confirm. Before turning on the device, it is necessary to send a restart signal to the relevant personnel to ensure that there are no workers in the operating area of the device. Then, slowly start the device and observe its operation. If everything is normal, resume normal production.
6. Record and analyze
Try to record in detail the occurrence of the fault, the process of handling it, and the subsequent operation status of the equipment. These data can help analyze the causes of faults, improve future operations and maintenance processes, and reduce the probability of similar faults happening again.
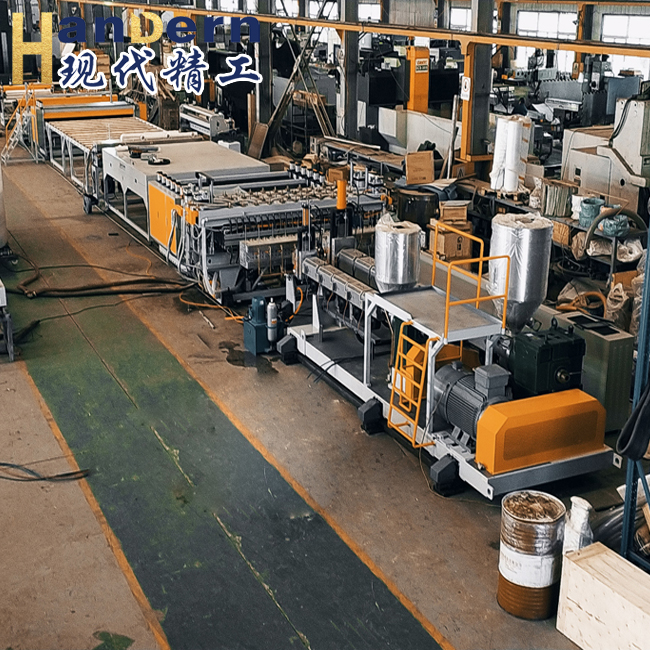
Before troubleshooting and handling faults, the first thing to ensure is the safety of operators and surrounding staff. Immediately stop other ongoing operations to avoid restarting the device and prevent accidental injury. In addition, the power supply of the relevant equipment should be kept off to ensure that there is no electricity in the operating area.
2. Check the cause of the malfunction
Emergency stop faults may be caused by various reasons, and operators need to conduct item by item inspections:
Emergency stop button: Check if the emergency stop button is pressed incorrectly or stuck. Usually, long pressing this button will cause the device to stop running.
Sensor malfunction: Check if there is a sensor malfunction or alarm. The failure of sensors may cause the equipment to stop running.
Electrical malfunction: Check the electrical system of the equipment, including power supply, cables, and contactors, to see if there are any short circuits or open circuits.
Mechanical failure: Check the mechanical components of the machine, including rollers, chains, and their drive systems, to ensure that they are not stuck or damaged.
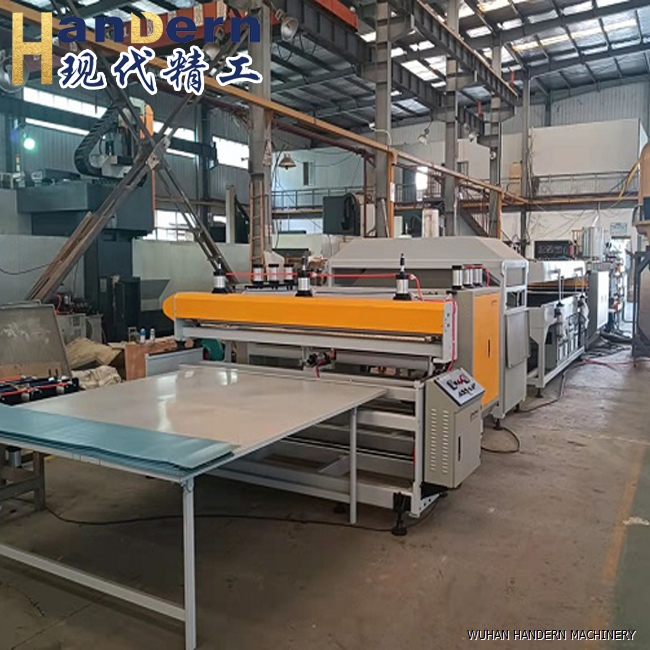
Search for fault codes and alarm information through the display information on the control panel. Many modern plastic hollow board pulling machines are equipped with displays that can provide detailed information about the reasons for downtime, facilitating troubleshooting.
4. Troubleshooting
After identifying the cause of the malfunction, handle it according to the nature of the problem:
Simple malfunction: If the emergency button is pressed incorrectly, reset the button and restart the device to see if it can operate normally.
Replace faulty parts: If sensors or electrical components are found to be damaged, the corresponding parts should be replaced in a timely manner and necessary debugging should be carried out.
Mechanical inspection and lubrication: If the shutdown is caused by mechanical jamming, it is necessary to manually inspect and clean the jamming material, and lubricate if necessary.
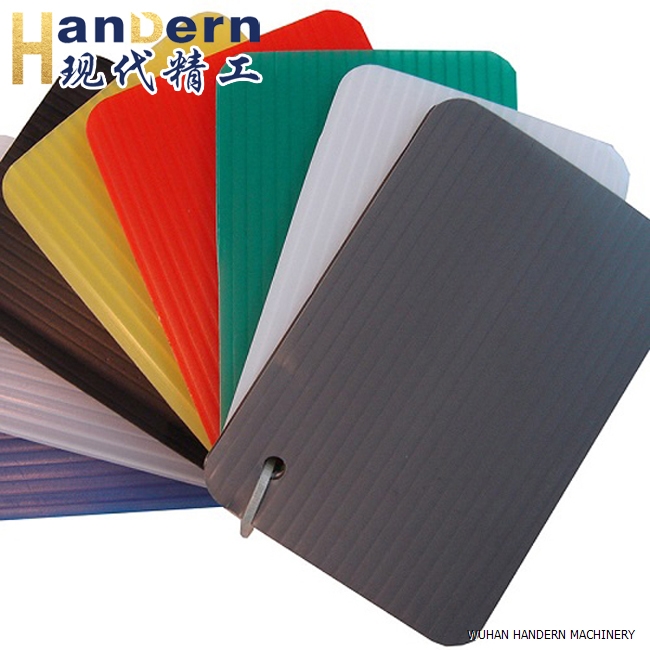
After resolving the malfunction, ensure that all safety measures are in place, ensure that the equipment is functioning properly, and conduct inspections to confirm. Before turning on the device, it is necessary to send a restart signal to the relevant personnel to ensure that there are no workers in the operating area of the device. Then, slowly start the device and observe its operation. If everything is normal, resume normal production.
6. Record and analyze
Try to record in detail the occurrence of the fault, the process of handling it, and the subsequent operation status of the equipment. These data can help analyze the causes of faults, improve future operations and maintenance processes, and reduce the probability of similar faults happening again.
Author:admin