How to build a factory building for a hollow board production line
DATE:2024/11/22 10:10:35 / READ: / SOURCE:This station
The construction of the hollow board production line is an important link in ensuring production efficiency, product quality, and safety. Reasonable factory design can not only optimize production processes, but also reduce operating costs. The following are several main requirements for the construction of hollow board production line factories:
1. Factory layout
The layout of the factory should follow the streamline of the production process to reduce material handling and improve production efficiency. Production lines typically include raw material storage areas, production and processing areas, finished product storage areas, and auxiliary facilities such as inspection rooms and employee rest areas. When designing, it is necessary to ensure smooth traffic between various functional areas to reduce material transportation time and cross flow of people, and improve production efficiency.
2. Security design
Safety is of paramount importance in factory construction. The factory building should be equipped with complete safety facilities, such as fire-fighting equipment, emergency evacuation signs, and emergency shutdown devices. At the same time, fire exits should be designed in accordance with local fire regulations to ensure that employees can evacuate quickly and safely in the event of an emergency. In addition, the structure of the factory building should be made of refractory materials and have a certain seismic resistance to ensure safety.
3. Ventilation and temperature control system
A good ventilation system is an important means of maintaining the air quality inside a factory building. Gas and heat are generated during the production process, so the factory should be designed with effective natural or mechanical ventilation systems to ensure air circulation and reduce internal temperature. In addition, appropriate temperature and humidity can improve production efficiency, reduce material deformation and quality issues during the production process.
4. Ground design
The ground design of the factory building should take into account load-bearing and anti slip properties. The production line equipment is heavy and subject to vibration, therefore the ground should be made of materials with sufficient load-bearing capacity, such as concrete. In addition, the ground should be kept flat and a well-designed drainage system should be implemented to prevent water from accumulating on the ground and reduce potential safety hazards.
5. Electricity and plumbing facilities
Hollow board production lines have high requirements for electricity and water sources. Reasonable power layout should be planned within the factory building to ensure the stability and safety of power supply, and to avoid production operations being affected by power issues. At the same time, the design of water pipes and drainage facilities should ensure real-time provision of clean water sources during the production process, as well as efficient treatment of production wastewater to avoid environmental pollution.
6. Environmental protection and sound insulation
With the increasingly strict environmental regulations, factory design should consider environmental requirements, adopt effective sound insulation measures, and reduce the impact of noise generated during the production process on the surrounding environment. In addition, exhaust gas treatment facilities should be installed to ensure that the gases emitted during the production process meet environmental standards.
7. Supporting facilities
The factory should also be equipped with basic supporting facilities, such as rest rooms, bathrooms, changing rooms, etc., to provide a good working environment for employees. This can not only enhance employees' work enthusiasm, but also improve the overall image of the company.
The construction of the hollow board production line requires comprehensive consideration of various requirements such as layout, safety, ventilation, temperature control, ground design, power and water pipe facilities, environmental protection, and employee supporting facilities. Through scientific planning and rational design, production efficiency can be effectively improved, product quality can be ensured, employee safety can be guaranteed, and the overall competitiveness of the enterprise can be enhanced.
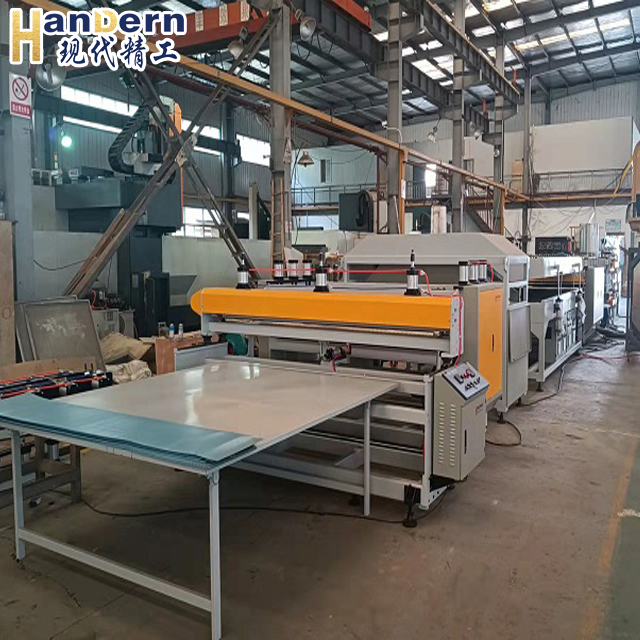
The layout of the factory should follow the streamline of the production process to reduce material handling and improve production efficiency. Production lines typically include raw material storage areas, production and processing areas, finished product storage areas, and auxiliary facilities such as inspection rooms and employee rest areas. When designing, it is necessary to ensure smooth traffic between various functional areas to reduce material transportation time and cross flow of people, and improve production efficiency.
2. Security design
Safety is of paramount importance in factory construction. The factory building should be equipped with complete safety facilities, such as fire-fighting equipment, emergency evacuation signs, and emergency shutdown devices. At the same time, fire exits should be designed in accordance with local fire regulations to ensure that employees can evacuate quickly and safely in the event of an emergency. In addition, the structure of the factory building should be made of refractory materials and have a certain seismic resistance to ensure safety.
3. Ventilation and temperature control system
A good ventilation system is an important means of maintaining the air quality inside a factory building. Gas and heat are generated during the production process, so the factory should be designed with effective natural or mechanical ventilation systems to ensure air circulation and reduce internal temperature. In addition, appropriate temperature and humidity can improve production efficiency, reduce material deformation and quality issues during the production process.
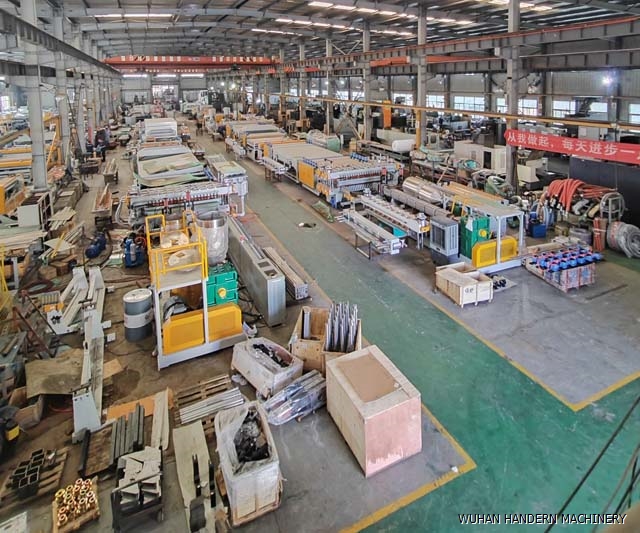
The ground design of the factory building should take into account load-bearing and anti slip properties. The production line equipment is heavy and subject to vibration, therefore the ground should be made of materials with sufficient load-bearing capacity, such as concrete. In addition, the ground should be kept flat and a well-designed drainage system should be implemented to prevent water from accumulating on the ground and reduce potential safety hazards.
5. Electricity and plumbing facilities
Hollow board production lines have high requirements for electricity and water sources. Reasonable power layout should be planned within the factory building to ensure the stability and safety of power supply, and to avoid production operations being affected by power issues. At the same time, the design of water pipes and drainage facilities should ensure real-time provision of clean water sources during the production process, as well as efficient treatment of production wastewater to avoid environmental pollution.
6. Environmental protection and sound insulation
With the increasingly strict environmental regulations, factory design should consider environmental requirements, adopt effective sound insulation measures, and reduce the impact of noise generated during the production process on the surrounding environment. In addition, exhaust gas treatment facilities should be installed to ensure that the gases emitted during the production process meet environmental standards.
7. Supporting facilities
The factory should also be equipped with basic supporting facilities, such as rest rooms, bathrooms, changing rooms, etc., to provide a good working environment for employees. This can not only enhance employees' work enthusiasm, but also improve the overall image of the company.
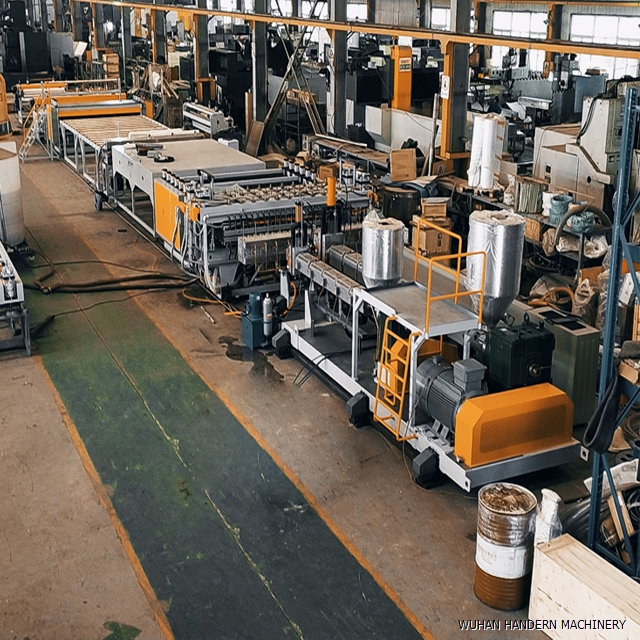
Author:admin