Common Fault Analysis of Plastic Hollow Board Production Equipment
DATE:2024/9/19 14:38:56 / READ: / SOURCE:This station
During the operation of plastic hollow board production equipment, various malfunctions may occur, affecting production efficiency and product quality. In order to prevent malfunctions and improve the ability to quickly solve them, we need to understand the common faults of the equipment. The following content will provide you with some of the main types of equipment faults, their possible causes, and solutions.
1. Difficulty starting the device
Reason: The device encountered difficulties during startup, which may be caused by power issues, control system failures, mechanical blockages, etc. Overloading during motor start-up or blown fuses may also cause this issue.
Solution suggestion: Check the wiring of the power circuit and motor to ensure that the power supply is functioning properly. At the same time, check the status of the control panel and related relays. If necessary, use a multimeter to measure current and voltage to ensure the normal operation of the motor and related components.
2. Unstable extruder flow rate
Reason: Fluctuations in extruder flow may be caused by uneven raw material particles, inaccurate temperature control, or screw wear. Blockage inside the material barrel and poor ventilation system may also cause abnormal flow.
Solution suggestion: Regularly check the quality of raw materials to ensure uniform particle size and avoid using contaminated or damp materials. At the same time, regularly maintain the extruder, clean the inside of the barrel, and ensure smooth ventilation.
3. Surface defects of the product
Reason: Scratches, bubbles, or dents on the surface of the produced hollow board may be related to the uneven surface of the mold, uneven temperature, or cooling system failure.
Solution suggestion: Regularly inspect the mold to ensure a smooth and clean surface. At the same time, monitor temperature changes during the production process to ensure the effective operation of heating and cooling systems. In addition, check the flow rate and temperature of the cooling water to ensure even cooling.
4. Overheating of the power system
Reason: Overheating of the power system may be caused by insufficient lubrication, excessive load, or fan failure. Frequent overload operation can also accelerate equipment aging.
Solution suggestion: Regularly check the lubrication condition of the power part to ensure timely replacement and addition of lubricating oil. Monitor the load situation of the equipment to avoid long-term overload operation. At the same time, check if the fan and cooling system are functioning properly to maintain proper heat dissipation of the equipment.
5. Unstable material head
Reason: The instability of the material head can lead to uneven width and thickness of the product, which may be caused by unstable pressure during the extrusion process or improper settings.
Solution suggestion: Monitor the pressure of the extruder to ensure it is within the predetermined range. At the same time, regularly calibrate the opening size of the mold to ensure good fit between the mold and the barrel.
6. Excessive equipment noise
Reason: Excessive equipment noise during the production process may be caused by mechanical wear, loose components, or poor installation.
Solution suggestion: Regularly inspect all components of the equipment to ensure that they are securely fastened without looseness, and check for friction and wear on mechanical parts. If necessary, replace or repair them.
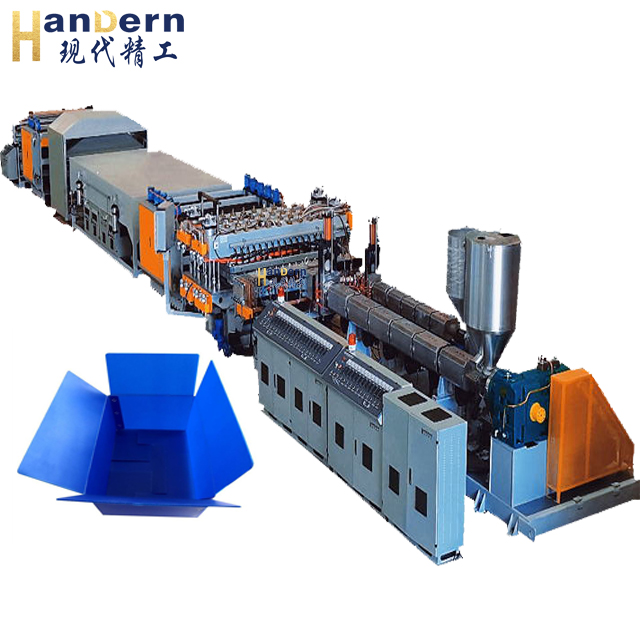
Reason: The device encountered difficulties during startup, which may be caused by power issues, control system failures, mechanical blockages, etc. Overloading during motor start-up or blown fuses may also cause this issue.
Solution suggestion: Check the wiring of the power circuit and motor to ensure that the power supply is functioning properly. At the same time, check the status of the control panel and related relays. If necessary, use a multimeter to measure current and voltage to ensure the normal operation of the motor and related components.
2. Unstable extruder flow rate
Reason: Fluctuations in extruder flow may be caused by uneven raw material particles, inaccurate temperature control, or screw wear. Blockage inside the material barrel and poor ventilation system may also cause abnormal flow.
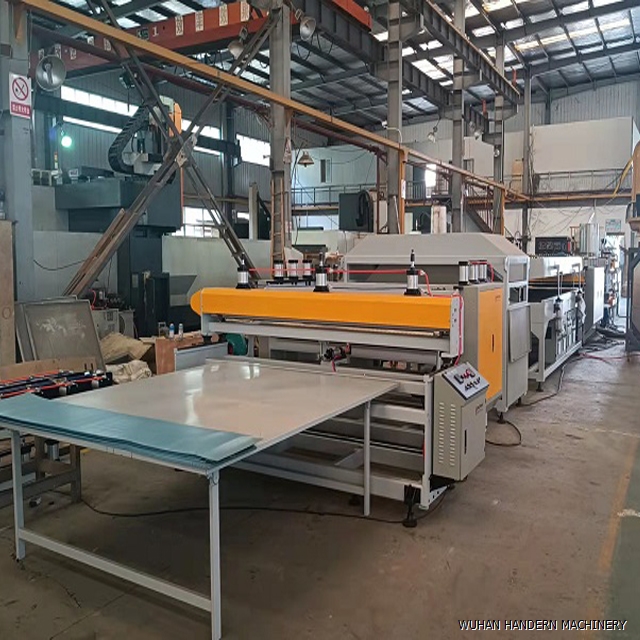
3. Surface defects of the product
Reason: Scratches, bubbles, or dents on the surface of the produced hollow board may be related to the uneven surface of the mold, uneven temperature, or cooling system failure.
Solution suggestion: Regularly inspect the mold to ensure a smooth and clean surface. At the same time, monitor temperature changes during the production process to ensure the effective operation of heating and cooling systems. In addition, check the flow rate and temperature of the cooling water to ensure even cooling.
4. Overheating of the power system
Reason: Overheating of the power system may be caused by insufficient lubrication, excessive load, or fan failure. Frequent overload operation can also accelerate equipment aging.
Solution suggestion: Regularly check the lubrication condition of the power part to ensure timely replacement and addition of lubricating oil. Monitor the load situation of the equipment to avoid long-term overload operation. At the same time, check if the fan and cooling system are functioning properly to maintain proper heat dissipation of the equipment.
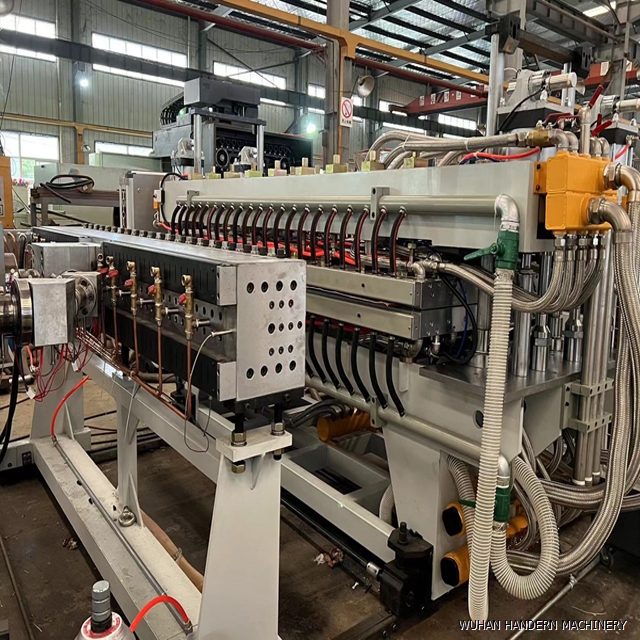
Reason: The instability of the material head can lead to uneven width and thickness of the product, which may be caused by unstable pressure during the extrusion process or improper settings.
Solution suggestion: Monitor the pressure of the extruder to ensure it is within the predetermined range. At the same time, regularly calibrate the opening size of the mold to ensure good fit between the mold and the barrel.
6. Excessive equipment noise
Reason: Excessive equipment noise during the production process may be caused by mechanical wear, loose components, or poor installation.
Solution suggestion: Regularly inspect all components of the equipment to ensure that they are securely fastened without looseness, and check for friction and wear on mechanical parts. If necessary, replace or repair them.
Author:admin