What details should be paid attention to when choosing a cast film production line
DATE:2024/9/18 15:36:49 / READ: / SOURCE:This station
The composition and structure of the cast film production line have diverse characteristics, which can be applied to various materials and produce various thin film products of different specifications. Therefore, when choosing a cast film production line, enterprises need to pay attention to multiple key details to ensure that the purchased equipment can meet production needs. Here are some important considerations:
1. Production capacity
Firstly, it is very important to clarify one's own production needs. This includes expected production volume, product specifications, and production cycle. The capacity of a cast film production line is usually calculated in tons per hour, and selecting appropriate equipment can ensure smooth production during peak demand periods without encountering bottlenecks.
2. Material compatibility
The production of cast film requires different types of plastic raw materials, such as polyethylene (PE), polypropylene (PP), etc. When choosing a production line, it is necessary to ensure that its design is compatible with the raw materials used. In addition, consider whether to support the application of different formulas and additives to meet the diverse needs of the market.
3. Technical parameters
It is very important to pay attention to the technical parameters of the casting film production line. Including melt index, temperature control range, efficiency of cooling system, etc. An efficient temperature control system can ensure the quality of the membrane, while precise pressure control can enhance production stability.
4. Equipment composition
A cast film production line usually consists of an extruder, a cast machine, a cooling system, a winding device, etc. Understand the technical specifications and quality of each component to ensure efficient operation at every stage, reduce failure rates, and improve production efficiency.
5. Degree of automation
The degree of automation in modern production lines directly affects production efficiency and labor costs. High degree automation can reduce manual intervention, lower the risk of human error, and improve production continuity and stability. When choosing, automatic feeding, automatic cutting, and automatic detection systems can be considered.
6. Energy consumption and efficiency
Energy consumption is an important consideration factor in the production process of cast film. Choosing energy-efficient equipment can not only reduce production costs, but also lower a company's carbon emissions. Pay attention to the energy consumption indicators and related certifications of the production line, and choose a sustainable and environmentally friendly solution.
7. Maintenance and after-sales service
Understanding the after-sales service and technical support provided by suppliers is also crucial. Choosing a supplier with a good reputation, able to provide timely maintenance and on-site service, can quickly restore production in case of equipment failure and avoid economic losses.
8. Cost and return on investment
For enterprises, the procurement cost and return on investment (ROI) of the casting film production line are also important considerations. When evaluating the total cost, in addition to procurement expenses, subsequent operating costs, maintenance costs, etc. should also be considered. Try to choose equipment with high cost-effectiveness to ensure the rationality of investment.
9. Enterprise scale and scalability
Finally, based on the current scale and future development plan of the enterprise, select a production line with certain scalability. If there is a possibility of expanding production demand in the future, it is recommended to choose equipment that can be upgraded or expanded to adapt to changes in the future market.
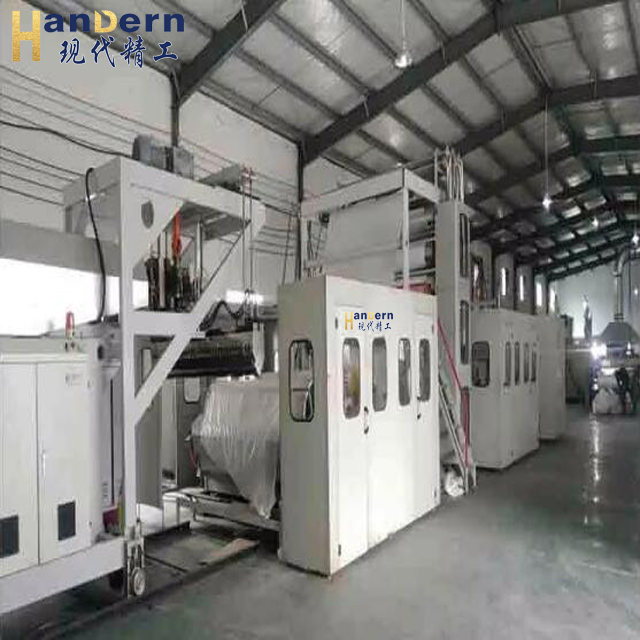
Firstly, it is very important to clarify one's own production needs. This includes expected production volume, product specifications, and production cycle. The capacity of a cast film production line is usually calculated in tons per hour, and selecting appropriate equipment can ensure smooth production during peak demand periods without encountering bottlenecks.
2. Material compatibility
The production of cast film requires different types of plastic raw materials, such as polyethylene (PE), polypropylene (PP), etc. When choosing a production line, it is necessary to ensure that its design is compatible with the raw materials used. In addition, consider whether to support the application of different formulas and additives to meet the diverse needs of the market.
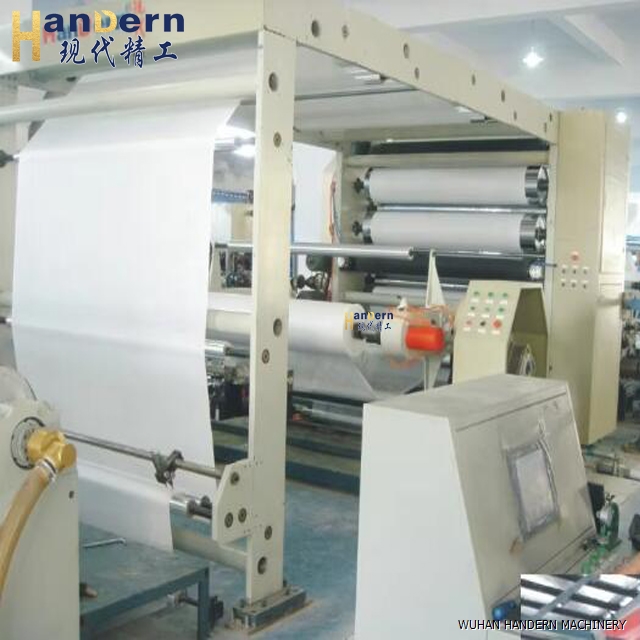
It is very important to pay attention to the technical parameters of the casting film production line. Including melt index, temperature control range, efficiency of cooling system, etc. An efficient temperature control system can ensure the quality of the membrane, while precise pressure control can enhance production stability.
4. Equipment composition
A cast film production line usually consists of an extruder, a cast machine, a cooling system, a winding device, etc. Understand the technical specifications and quality of each component to ensure efficient operation at every stage, reduce failure rates, and improve production efficiency.
5. Degree of automation
The degree of automation in modern production lines directly affects production efficiency and labor costs. High degree automation can reduce manual intervention, lower the risk of human error, and improve production continuity and stability. When choosing, automatic feeding, automatic cutting, and automatic detection systems can be considered.
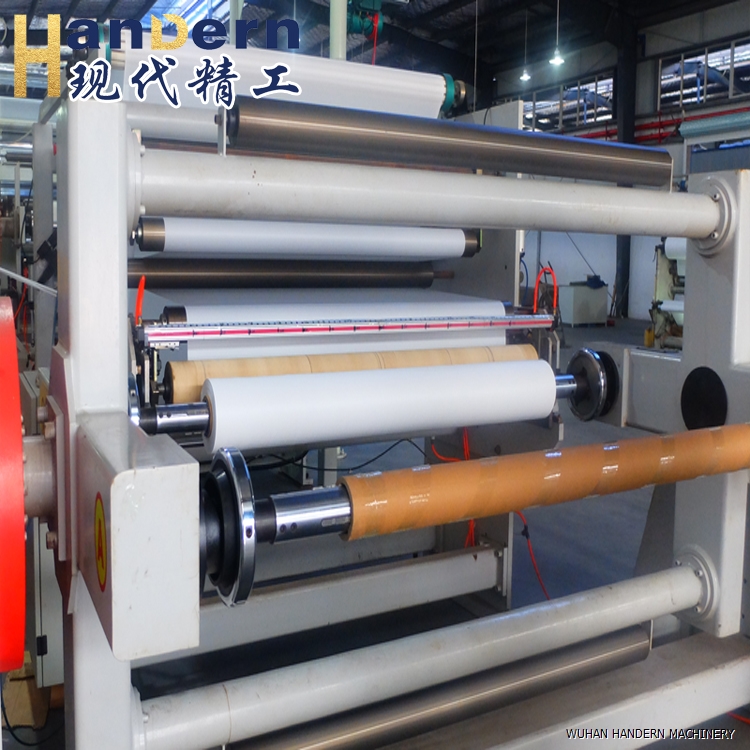
Energy consumption is an important consideration factor in the production process of cast film. Choosing energy-efficient equipment can not only reduce production costs, but also lower a company's carbon emissions. Pay attention to the energy consumption indicators and related certifications of the production line, and choose a sustainable and environmentally friendly solution.
7. Maintenance and after-sales service
Understanding the after-sales service and technical support provided by suppliers is also crucial. Choosing a supplier with a good reputation, able to provide timely maintenance and on-site service, can quickly restore production in case of equipment failure and avoid economic losses.
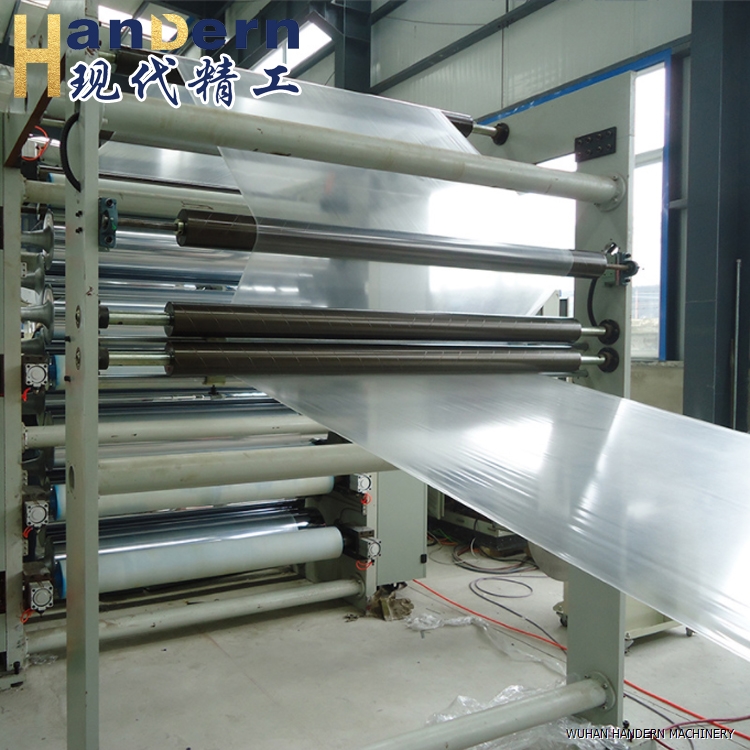
For enterprises, the procurement cost and return on investment (ROI) of the casting film production line are also important considerations. When evaluating the total cost, in addition to procurement expenses, subsequent operating costs, maintenance costs, etc. should also be considered. Try to choose equipment with high cost-effectiveness to ensure the rationality of investment.
9. Enterprise scale and scalability
Finally, based on the current scale and future development plan of the enterprise, select a production line with certain scalability. If there is a possibility of expanding production demand in the future, it is recommended to choose equipment that can be upgraded or expanded to adapt to changes in the future market.
Author:admin