What are plastic stone paper blown film production line and cast film production line
DATE:2024/11/26 10:25:52 / READ: / SOURCE:This station
Plastic stone paper is a new type of environmentally friendly material, mainly made by mixing biodegradable materials such as calcium carbonate and polyethylene, which combines the advantages of paper and plastic. In order to meet market demand, the production of plastic stone paper usually adopts two main production processes: blown film and cast film. The following provides a detailed introduction to the characteristics and process flow of these two production lines.
Plastic stone paper blown film production line
1. Process flow
The plastic stone paper blown film production line mainly consists of raw material conveying system, extruder, mold, cooling system, traction and winding device, etc. The process flow is as follows:
Raw material processing: Mix calcium carbonate and polyethylene in a certain proportion, dry them, and send them into an extruder.
Extrusion: In an extruder, the raw materials are heated, mixed, and melted to form a uniform molten plastic.
Blowing film: The molten material is extruded through a circular mold to form a thin film tube. Then, the film is slowly cooled and solidified through air expansion and cooling.
Traction and winding: The cooled film is wound into a roll by a traction device.
2. Advantages
High production efficiency: The blown film process can quickly produce high-quality films and meet the needs of large-scale production.
Good physical properties: By adjusting the formula and blown film process, high mechanical strength and transparency can be achieved.
Environmental friendliness: The raw materials of stone paper are produced in a wood free manner, reducing dependence on trees and contributing to environmental protection.
Plastic Stone Paper Casting Production Line
1. Process flow
The casting production line mainly consists of raw material pretreatment, extruder, casting mold, cooling device, trimming and winding system, etc. The process flow is as follows:
Raw material preparation: Similar to the blown film production line, first mix calcium carbonate with polyethylene.
Melt extrusion: Heating and melting in an extruder to form a uniform molten fluid.
Casting molding: Molten material is extruded through a casting die to form a flat film. At this point, the thickness and width of the film can be controlled by adjusting the speed of the casting machine and the temperature of the mold.
Cooling: The molten film is rapidly cooled and formed through a cooling roller or air cooling device.
Cutting and winding: The cooled film is cut into the required specifications and rolled.
2. Advantages
High quality surface: During the casting production process, the consistency and smoothness of the film are high, making it suitable for some high-end packaging and printing applications.
Flexibility: The thickness and width of the film can be adjusted according to different market demands.
Significant energy-saving effect: The casting process is relatively simple, and the required energy consumption is usually lower than that of blown film.
The blown film and cast film production lines for plastic stone paper each have their own advantages and disadvantages. The blown film production line is more suitable for efficient and large-scale production needs, while the cast film production line performs better in terms of product surface quality and customization. The choice between the two often depends on the intended use of the final product and market demand. In practical applications, appropriate production methods can improve product quality, reduce production costs, and thus gain an advantage in an increasingly competitive market. With the increasing demand for environmentally friendly materials, the production technology of plastic stone paper is also constantly improving, and it will have a wider range of application prospects in the future.

1. Process flow
The plastic stone paper blown film production line mainly consists of raw material conveying system, extruder, mold, cooling system, traction and winding device, etc. The process flow is as follows:
Raw material processing: Mix calcium carbonate and polyethylene in a certain proportion, dry them, and send them into an extruder.
Extrusion: In an extruder, the raw materials are heated, mixed, and melted to form a uniform molten plastic.
Blowing film: The molten material is extruded through a circular mold to form a thin film tube. Then, the film is slowly cooled and solidified through air expansion and cooling.
Traction and winding: The cooled film is wound into a roll by a traction device.
2. Advantages
High production efficiency: The blown film process can quickly produce high-quality films and meet the needs of large-scale production.
Good physical properties: By adjusting the formula and blown film process, high mechanical strength and transparency can be achieved.
Environmental friendliness: The raw materials of stone paper are produced in a wood free manner, reducing dependence on trees and contributing to environmental protection.
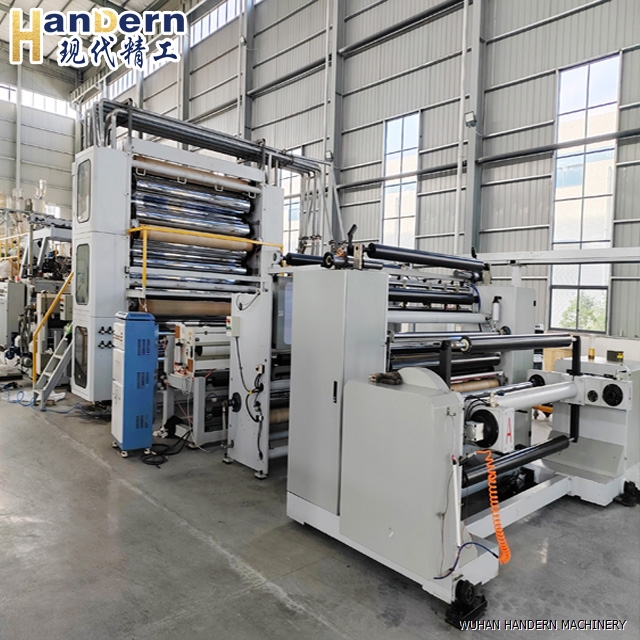
1. Process flow
The casting production line mainly consists of raw material pretreatment, extruder, casting mold, cooling device, trimming and winding system, etc. The process flow is as follows:
Raw material preparation: Similar to the blown film production line, first mix calcium carbonate with polyethylene.
Melt extrusion: Heating and melting in an extruder to form a uniform molten fluid.
Casting molding: Molten material is extruded through a casting die to form a flat film. At this point, the thickness and width of the film can be controlled by adjusting the speed of the casting machine and the temperature of the mold.
Cooling: The molten film is rapidly cooled and formed through a cooling roller or air cooling device.
Cutting and winding: The cooled film is cut into the required specifications and rolled.
2. Advantages
High quality surface: During the casting production process, the consistency and smoothness of the film are high, making it suitable for some high-end packaging and printing applications.
Flexibility: The thickness and width of the film can be adjusted according to different market demands.
Significant energy-saving effect: The casting process is relatively simple, and the required energy consumption is usually lower than that of blown film.
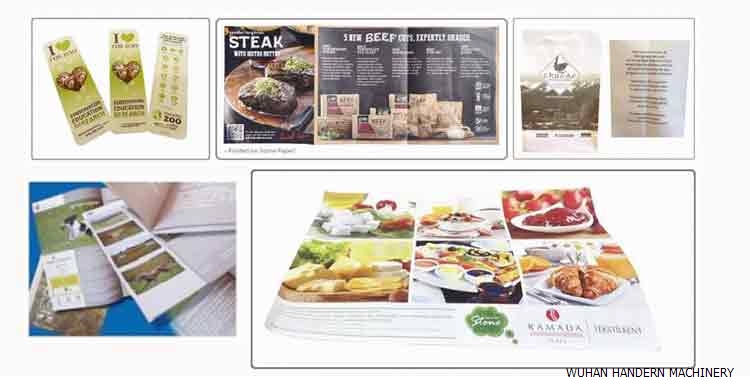
Author:admin