What is the difference between single screw and twin-screw plastic extruders
DATE:2024/11/18 11:17:03 / READ: / SOURCE:This station
Plastic extruders are widely used in the plastic processing industry, mainly producing various plastic products by heating, melting, and extruding plastic materials. Among them, single screw extruder and twin-screw extruder are two common types, which have significant differences in structure, working principle, applicability, and processing performance. The differences between the two will be discussed in detail below.
1. Structure
A single screw extruder consists of a screw and a cylinder, and the rotation of the screw drives the plastic material to advance along the groove of the screw. As the screw rotates, the plastic material is gradually extruded under the thrust and shear of the screw.
A twin-screw extruder consists of two parallel or staggered screws that can rotate clockwise or counterclockwise. The structure of twin-screw extruders allows for more uniform shearing and mixing of plastics during the extrusion process, resulting in higher melting and mixing efficiency than single screw extruders.
2. Working principle
The single screw extruder mainly relies on the pushing force and friction force of the screw to feed the raw material into the extrusion outlet. During the rotation of the screw, the material is gradually heated and melted, and then extruded through the nozzle. This design is suitable for handling plastics with good fluidity, such as polyethylene (PE) and polypropylene (PP).
The twin-screw extruder provides better material mixing and melting effects due to the interaction between the two screws. Twin screws can perform more complex processing techniques such as blending, reactive extrusion, and filling processes, effectively handling plastics containing additives or pigments.
3. Scope of application
Single screw extruders are commonly used to produce plastic products with relatively single raw materials and low viscosity, such as films, pipes, and sheets. Its equipment cost is relatively low, the operation is simple, and it is suitable for large-scale production.
Twin screw extruders are suitable for processing complex plastic materials, such as engineering plastics, composite materials, modified plastics, etc. It can provide higher processing temperature and pressure, suitable for processing materials with high viscosity and high dispersion, especially when high uniformity mixing and melting are required, twin-screw extruders have more advantages.
4. Processing performance
In terms of processing performance, twin-screw extruders have higher plasticizing ability, stronger mixing effect, and faster output. Due to the interaction between twin-screw, materials with a large proportion of additives can be better processed. Single screw extruders are more direct and convenient to operate, suitable for processing scenarios that do not require high temperature control.
5. Cost and Maintenance
The equipment cost of a single screw extruder is relatively low and maintenance is relatively simple, but its processing flexibility and range are limited. However, twin-screw extruders have higher equipment investment and maintenance costs, but due to their higher production efficiency and multifunctionality, they often have an advantage in overall operating costs.
Single screw extruders and twin-screw extruders have their own characteristics in terms of structure, working principle, scope of application, processing performance, and cost. Single screw is suitable for simple and high-yield production of plastic products, while twin-screw performs better in applications with complex material handling and high mixing requirements. The selection of the appropriate extruder type depends on specific production needs and goals.
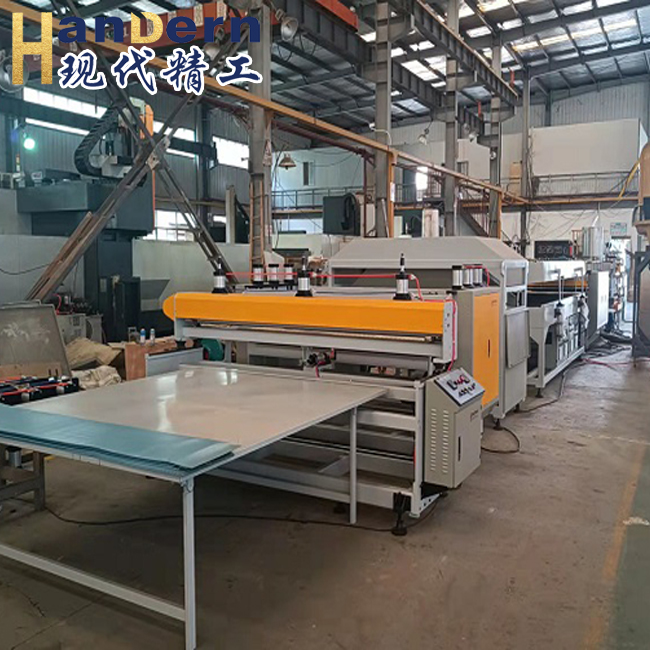
A single screw extruder consists of a screw and a cylinder, and the rotation of the screw drives the plastic material to advance along the groove of the screw. As the screw rotates, the plastic material is gradually extruded under the thrust and shear of the screw.
A twin-screw extruder consists of two parallel or staggered screws that can rotate clockwise or counterclockwise. The structure of twin-screw extruders allows for more uniform shearing and mixing of plastics during the extrusion process, resulting in higher melting and mixing efficiency than single screw extruders.
2. Working principle
The single screw extruder mainly relies on the pushing force and friction force of the screw to feed the raw material into the extrusion outlet. During the rotation of the screw, the material is gradually heated and melted, and then extruded through the nozzle. This design is suitable for handling plastics with good fluidity, such as polyethylene (PE) and polypropylene (PP).
The twin-screw extruder provides better material mixing and melting effects due to the interaction between the two screws. Twin screws can perform more complex processing techniques such as blending, reactive extrusion, and filling processes, effectively handling plastics containing additives or pigments.
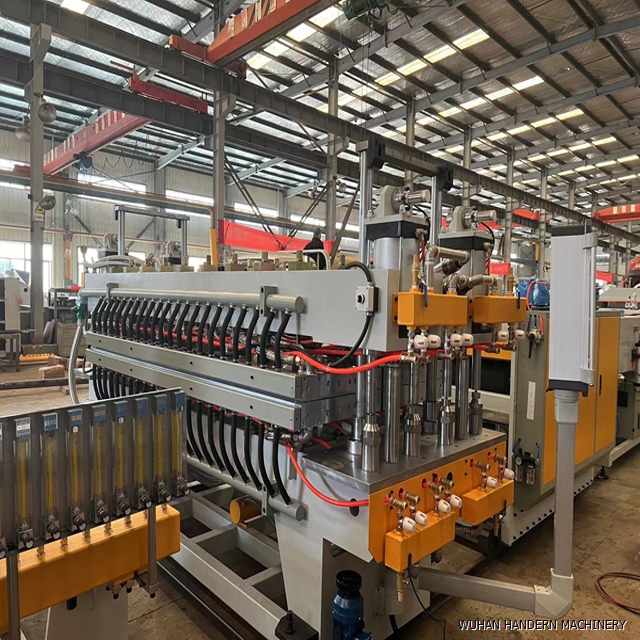
Single screw extruders are commonly used to produce plastic products with relatively single raw materials and low viscosity, such as films, pipes, and sheets. Its equipment cost is relatively low, the operation is simple, and it is suitable for large-scale production.
Twin screw extruders are suitable for processing complex plastic materials, such as engineering plastics, composite materials, modified plastics, etc. It can provide higher processing temperature and pressure, suitable for processing materials with high viscosity and high dispersion, especially when high uniformity mixing and melting are required, twin-screw extruders have more advantages.
4. Processing performance
In terms of processing performance, twin-screw extruders have higher plasticizing ability, stronger mixing effect, and faster output. Due to the interaction between twin-screw, materials with a large proportion of additives can be better processed. Single screw extruders are more direct and convenient to operate, suitable for processing scenarios that do not require high temperature control.
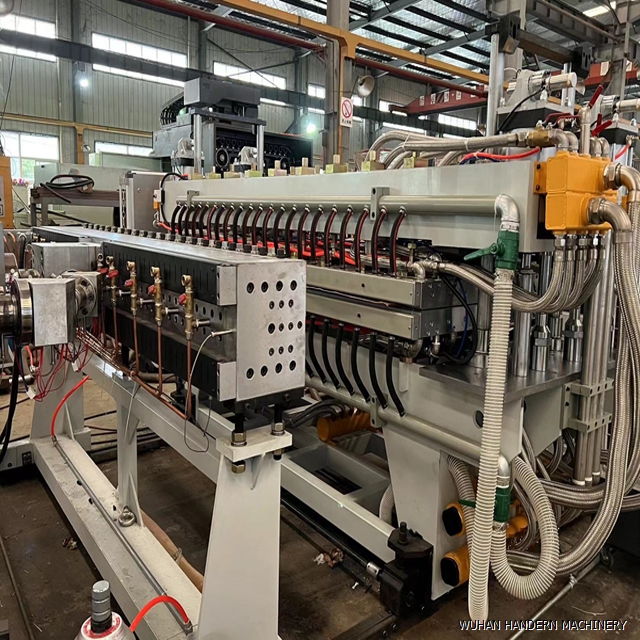
The equipment cost of a single screw extruder is relatively low and maintenance is relatively simple, but its processing flexibility and range are limited. However, twin-screw extruders have higher equipment investment and maintenance costs, but due to their higher production efficiency and multifunctionality, they often have an advantage in overall operating costs.
Single screw extruders and twin-screw extruders have their own characteristics in terms of structure, working principle, scope of application, processing performance, and cost. Single screw is suitable for simple and high-yield production of plastic products, while twin-screw performs better in applications with complex material handling and high mixing requirements. The selection of the appropriate extruder type depends on specific production needs and goals.
Author:admin