What kind of plastic hollow board belongs to qualified products
DATE:2024/10/30 11:27:21 / READ: / SOURCE:This station
Plastic hollow board is a new type of environmentally friendly material widely used in packaging, advertising, construction, furniture and other fields. In order to ensure good performance and meet practical application requirements, qualified plastic hollow boards must possess the following key characteristics.
1. Material composition
Qualified plastic hollow boards are usually made of high-quality polypropylene (PP) or polyethylene (PE) materials. These materials should comply with national or industry standards, and no harmful substances such as heavy metals and toxic plasticizers should be added during the production process. In addition, manufacturers should be able to provide relevant material testing reports to demonstrate the environmental friendliness and safety of their materials.
2. Physical properties
Qualified plastic hollow boards should have good physical properties, including compressive strength, impact resistance, and wear resistance. These performances can be tested through the following indicators:
Compressive strength: Hollow boards should not undergo significant deformation or breakage under stress, and their compressive performance can usually be evaluated through laboratory testing.
Impact resistance: Hollow boards should have sufficient toughness to withstand external impacts without cracking or breaking.
Temperature resistance: Qualified hollow boards should be able to maintain stability within a certain temperature range, without deformation or damage due to high or low temperatures.
3. Size and appearance
Qualified plastic hollow boards should be strictly controlled in size during the production process to ensure consistency in thickness and length. The common qualified value is within the thickness range of 1.8mm to 12mm, depending on the application requirements. At the same time, the appearance should be smooth and flat, without obvious bubbles, scratches or other defects.
4. Environmental certification
More and more customers are demanding higher environmental performance, therefore, qualified plastic hollow boards should usually obtain some environmental certifications, such as ISO 14001, ROHS, or REACH. These certifications can prove that the product has a minimal impact on the environment throughout its lifecycle, thereby enhancing its market competitiveness.
5. Flame retardant performance
For certain specific applications, such as use in the construction industry, qualified plastic hollow boards should also have certain flame retardant properties. According to national standards, the flame retardant rating should meet the corresponding requirements to ensure safety in emergency situations such as fires.
6. Production process
The process of producing hollow boards also directly affects their quality. Qualified plastic hollow boards usually use high standard extrusion technology and mature production processes to ensure their stability and consistency; At the same time, temperature, pressure and other parameters should be strictly controlled during the production process to avoid material overheating and degradation.
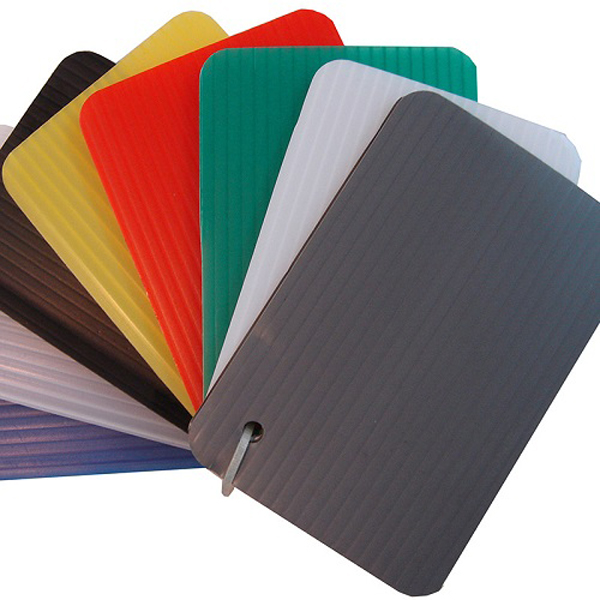
Qualified plastic hollow boards are usually made of high-quality polypropylene (PP) or polyethylene (PE) materials. These materials should comply with national or industry standards, and no harmful substances such as heavy metals and toxic plasticizers should be added during the production process. In addition, manufacturers should be able to provide relevant material testing reports to demonstrate the environmental friendliness and safety of their materials.
2. Physical properties
Qualified plastic hollow boards should have good physical properties, including compressive strength, impact resistance, and wear resistance. These performances can be tested through the following indicators:
Compressive strength: Hollow boards should not undergo significant deformation or breakage under stress, and their compressive performance can usually be evaluated through laboratory testing.
Impact resistance: Hollow boards should have sufficient toughness to withstand external impacts without cracking or breaking.
Temperature resistance: Qualified hollow boards should be able to maintain stability within a certain temperature range, without deformation or damage due to high or low temperatures.
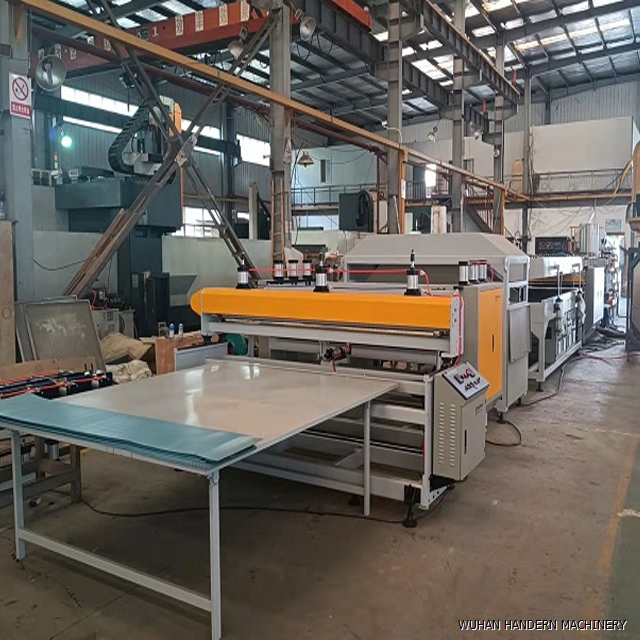
Qualified plastic hollow boards should be strictly controlled in size during the production process to ensure consistency in thickness and length. The common qualified value is within the thickness range of 1.8mm to 12mm, depending on the application requirements. At the same time, the appearance should be smooth and flat, without obvious bubbles, scratches or other defects.
4. Environmental certification
More and more customers are demanding higher environmental performance, therefore, qualified plastic hollow boards should usually obtain some environmental certifications, such as ISO 14001, ROHS, or REACH. These certifications can prove that the product has a minimal impact on the environment throughout its lifecycle, thereby enhancing its market competitiveness.
5. Flame retardant performance
For certain specific applications, such as use in the construction industry, qualified plastic hollow boards should also have certain flame retardant properties. According to national standards, the flame retardant rating should meet the corresponding requirements to ensure safety in emergency situations such as fires.
6. Production process
The process of producing hollow boards also directly affects their quality. Qualified plastic hollow boards usually use high standard extrusion technology and mature production processes to ensure their stability and consistency; At the same time, temperature, pressure and other parameters should be strictly controlled during the production process to avoid material overheating and degradation.
Author:admin