What are the configurations of equipment available for making plastic hollow boards
DATE:2024/10/16 10:48:16 / READ: / SOURCE:This station
Plastic hollow board is made of plastic materials such as polypropylene (PP) and is widely used in packaging, advertising, construction, furniture and other fields. The production of this hollow board requires various equipment, which varies depending on factors such as production scale, technical requirements, and product specifications. Here are some common equipment models and related instructions for producing plastic hollow boards:
1. Extruder
The extruder is the core equipment for producing plastic hollow boards, responsible for melting and extruding plastic raw materials into shapes. Common extruder models include:
Single screw extruder (model such as SJ series): suitable for the production of general hollow boards, easy to operate, and suitable for lower production requirements. Has good plasticizing ability and economy.
Twin screw extruder (model such as SG series): suitable for production lines with higher requirements for molten materials, capable of achieving higher mixing uniformity and material modification. Suitable for higher grade hollow board products.
2. Mold head
The die head is a key component of the extruder, used to shape molten plastic into hollow plates. Different die models are suitable for products of different thicknesses and widths. Common mold head models include:
Flat die head (such as T-shaped die head): commonly used in the production of flat hollow boards, which can effectively control the width and thickness of the board.
Spiral die head: suitable for the production of hollow boards with special shapes or structures, providing a more uniform thickness distribution.
3. Cooling system
The cooling system is used for rapid cooling and shaping of hollow boards after extrusion, usually including a water tank and air cooling equipment:
Water cooling tank (customizable model): By circulating water, the plastic hollow board is quickly cooled to maintain the shape and size of the product.
Air cooling device: Some production lines are also equipped with air cooling systems, which provide additional cooling for products through fans.
4. Traction machine
The traction machine is used to pull the extruded hollow board out of the mold. Common models include:
The cutting machine is used to cut the produced hollow board into the required length. Common cutting machine models include:
For hollow boards that require printing or special processing, equipment such as:
Screen printing machine (model such as YS series): prints patterns onto the surface of hollow boards to enhance product aesthetics.
Film laminating machine (model such as FL series): used to film the surface of hollow boards to improve waterproof and dustproof effects.
7. Other auxiliary equipment
In addition, the production of hollow boards also requires some other auxiliary equipment, including:
Drying machine: used for drying raw materials to avoid affecting the plasticizing effect due to excessive moisture.
Hopper feeder: Ensure uniform supply of raw materials during the extrusion process.
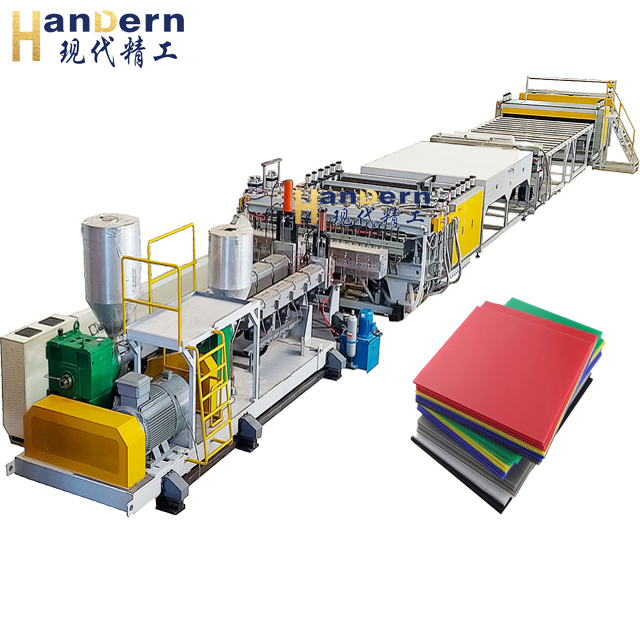
The extruder is the core equipment for producing plastic hollow boards, responsible for melting and extruding plastic raw materials into shapes. Common extruder models include:
Single screw extruder (model such as SJ series): suitable for the production of general hollow boards, easy to operate, and suitable for lower production requirements. Has good plasticizing ability and economy.
Twin screw extruder (model such as SG series): suitable for production lines with higher requirements for molten materials, capable of achieving higher mixing uniformity and material modification. Suitable for higher grade hollow board products.
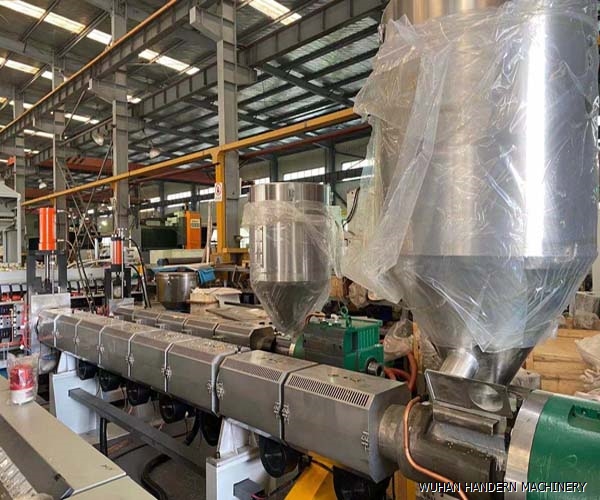
The die head is a key component of the extruder, used to shape molten plastic into hollow plates. Different die models are suitable for products of different thicknesses and widths. Common mold head models include:
Flat die head (such as T-shaped die head): commonly used in the production of flat hollow boards, which can effectively control the width and thickness of the board.
Spiral die head: suitable for the production of hollow boards with special shapes or structures, providing a more uniform thickness distribution.
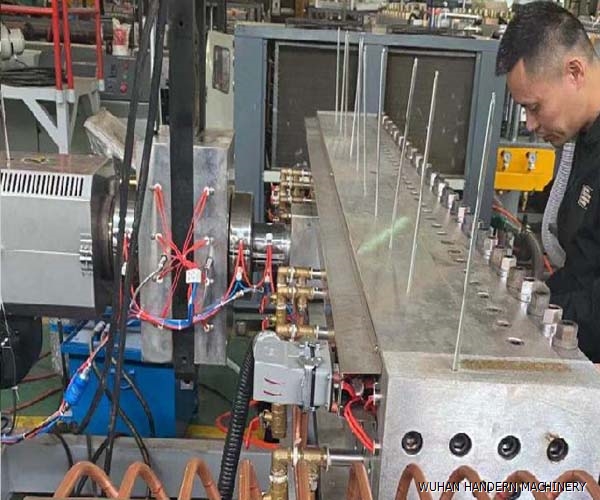
The cooling system is used for rapid cooling and shaping of hollow boards after extrusion, usually including a water tank and air cooling equipment:
Water cooling tank (customizable model): By circulating water, the plastic hollow board is quickly cooled to maintain the shape and size of the product.
Air cooling device: Some production lines are also equipped with air cooling systems, which provide additional cooling for products through fans.
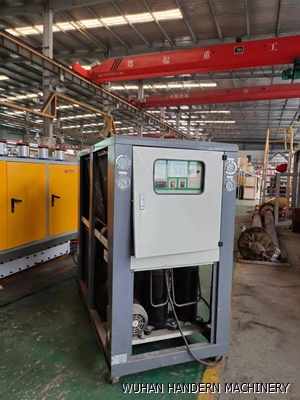
The traction machine is used to pull the extruded hollow board out of the mold. Common models include:
High speed tractor (model such as TY series): suitable for large-scale, high-speed production, with good effects on the stretching and thickness control of hollow boards.
The cutting machine is used to cut the produced hollow board into the required length. Common cutting machine models include:
Automatic cutting machine (model such as QX series): capable of automatically cutting according to the set length, improving production efficiency.
For hollow boards that require printing or special processing, equipment such as:
Screen printing machine (model such as YS series): prints patterns onto the surface of hollow boards to enhance product aesthetics.
Film laminating machine (model such as FL series): used to film the surface of hollow boards to improve waterproof and dustproof effects.
7. Other auxiliary equipment
In addition, the production of hollow boards also requires some other auxiliary equipment, including:
Drying machine: used for drying raw materials to avoid affecting the plasticizing effect due to excessive moisture.
Hopper feeder: Ensure uniform supply of raw materials during the extrusion process.
Author:admin