Introduction to PEN Cast Film Production Line and Its Products
DATE:2024/10/10 11:05:00 / READ: / SOURCE:This station
PEN film is a type of film made by polymerizing poly (naphthalene dicarboxylic acid) and ethylene glycol. The commonly used production process is to produce a film by casting molten polymer through a casting method, which results in a film with good physical and chemical properties. At present, PEN film is mainly used in the baseband of magnetic tapes, flexible printed circuit boards, capacitor films, F-class insulation films, and other fields.
1、 Characteristics of PEN cast film
High thermal stability: Compared to other polyester films such as PET, PEN cast film can maintain its mechanical properties and morphological stability at higher temperatures.
Excellent transparency: PEN cast film has good light transmittance and can be used in various optical applications.
Excellent gas barrier properties: PEN cast film has low oxygen and water vapor transmission rates, making it suitable for food and pharmaceutical packaging and improving product preservation capabilities.
Good chemical stability: Strong resistance to many solvents, acids, and bases, suitable for use in chemical environments.
Superior mechanical performance: PEN cast film has high tensile strength and toughness, and can withstand large external forces.
2、 Production steps of PEN cast film
Aggregation: Synthesize a polymer of naphthalene dicarboxylic acid and ethylene glycol through a condensation reaction based on the required molecular weight and formula.
Melt extrusion: Heating the synthesized polymer to a molten state and extruding it through an extruder.
Casting molding: Molten polymer is cast into a thin film state on a cooling roller through a casting machine, and after cooling, a thin film is formed.
Post processing: Annealing, cutting and other post-processing processes can be carried out to achieve the specified thickness and performance.
3、 Characteristics of PEN Cast Film Production Line
1. The entire line adopts servo motors for precision extrusion, accurate temperature control, and stable plasticization; Screw is resistant to high temperature, corrosion, and high hardness; The barrel temperature is 450 ° C.
2. Hanger style flow channel mold head, no need to disassemble the mold, directly remove the screw for cleaning. In addition, the discharge is uniform, there is no material stagnation/high hardness, and corrosion-resistant.
3. All three rollers are equipped with mold temperature machines, and the inner flow channel is specially designed to ensure temperature balance on the roller surface; The adjustable casting roller can meet the casting and forming needs of various materials.
4. The screw, barrel, die head, and casting auxiliary machine have all undergone special treatment to meet the needs of high-temperature material forming.
5. The production line is equipped with an online quality monitoring and control system to ensure the product qualification rate.
6. The entire line adopts PLC fully automatic control and is finally integrated into HMI touch screen terminals, with highly intelligent operation that saves labor costs.
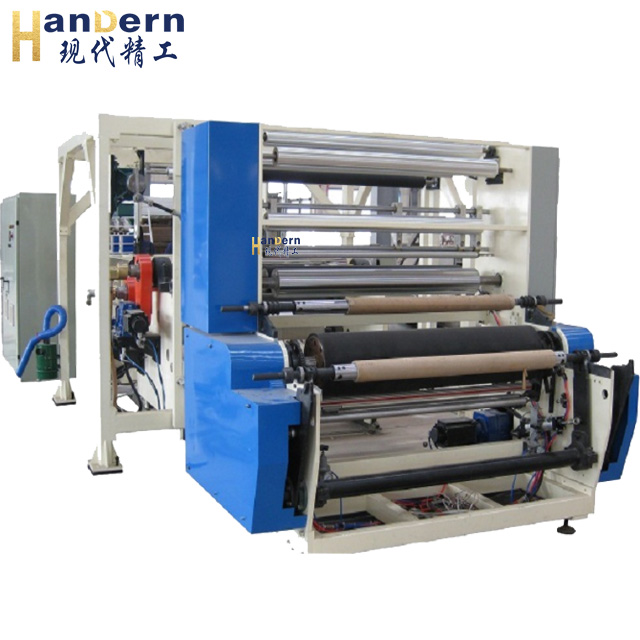
High thermal stability: Compared to other polyester films such as PET, PEN cast film can maintain its mechanical properties and morphological stability at higher temperatures.
Excellent transparency: PEN cast film has good light transmittance and can be used in various optical applications.
Excellent gas barrier properties: PEN cast film has low oxygen and water vapor transmission rates, making it suitable for food and pharmaceutical packaging and improving product preservation capabilities.
Good chemical stability: Strong resistance to many solvents, acids, and bases, suitable for use in chemical environments.
Superior mechanical performance: PEN cast film has high tensile strength and toughness, and can withstand large external forces.
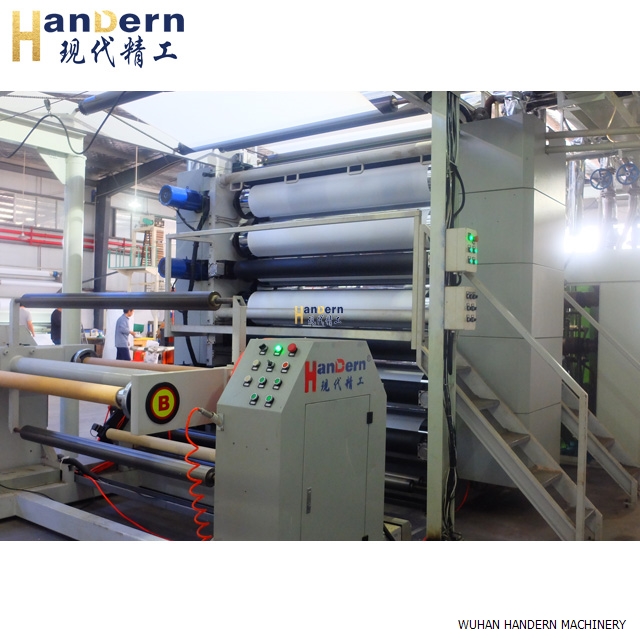
Aggregation: Synthesize a polymer of naphthalene dicarboxylic acid and ethylene glycol through a condensation reaction based on the required molecular weight and formula.
Melt extrusion: Heating the synthesized polymer to a molten state and extruding it through an extruder.
Casting molding: Molten polymer is cast into a thin film state on a cooling roller through a casting machine, and after cooling, a thin film is formed.
Post processing: Annealing, cutting and other post-processing processes can be carried out to achieve the specified thickness and performance.
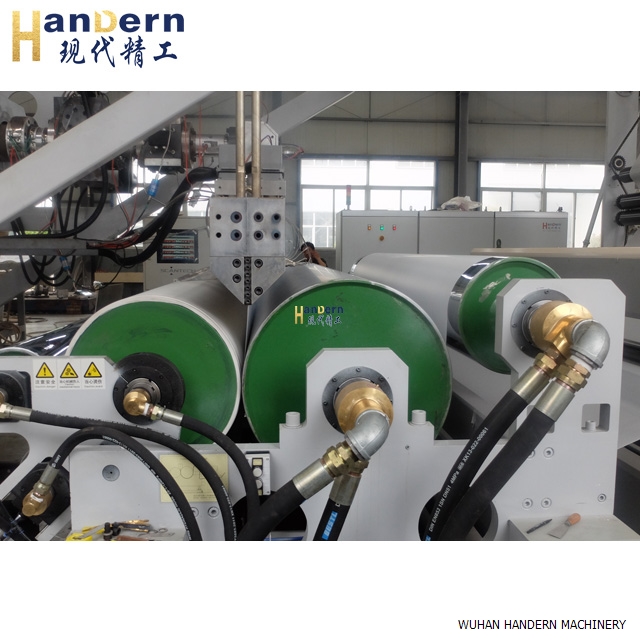
1. The entire line adopts servo motors for precision extrusion, accurate temperature control, and stable plasticization; Screw is resistant to high temperature, corrosion, and high hardness; The barrel temperature is 450 ° C.
2. Hanger style flow channel mold head, no need to disassemble the mold, directly remove the screw for cleaning. In addition, the discharge is uniform, there is no material stagnation/high hardness, and corrosion-resistant.
3. All three rollers are equipped with mold temperature machines, and the inner flow channel is specially designed to ensure temperature balance on the roller surface; The adjustable casting roller can meet the casting and forming needs of various materials.
4. The screw, barrel, die head, and casting auxiliary machine have all undergone special treatment to meet the needs of high-temperature material forming.
5. The production line is equipped with an online quality monitoring and control system to ensure the product qualification rate.
6. The entire line adopts PLC fully automatic control and is finally integrated into HMI touch screen terminals, with highly intelligent operation that saves labor costs.
Author:admin