What is diaphragm casting and stretching equipment
DATE:2024/10/8 14:41:19 / READ: / SOURCE:This station
Diaphragm casting and stretching equipment is a specialized device for producing high-performance polymer films, widely used in industries such as packaging, electronics, and photovoltaics. This device produces film products with specific properties, such as film separators and functional packaging films, through two main processes: casting and stretching. Below, we will provide a detailed introduction from multiple aspects such as device structure, working principle, application fields, and advantages.
1. Equipment construction
The diaphragm casting and stretching equipment mainly consists of the following parts:
Extruder: Heat and melt plastic resin, and extrude it into a film through a screw. This section is usually equipped with a temperature control system to ensure the stability of the molten state.
Casting mold: used to rapidly solidify molten plastic into thin films, its design directly affects the thickness and uniformity of the film. Molds generally use cooling systems to accelerate the cooling and solidification process of molten plastics.
Cooling device: By means of air cooling or water cooling, the initially formed film is rapidly cooled to maintain its shape and performance.
Stretching device: including a longitudinal stretching machine and a transverse stretching machine, which apply tensile force to the film to change its physical and chemical properties. The stretching process can improve the mechanical strength and barrier properties of the film.
Winding equipment: Roll the stretched film into a roll for subsequent processing and transportation.
2. Working principle
The production of thin films by membrane casting and stretching equipment is suitable for multiple industries:
Electronics industry: Used for manufacturing separators for polymer lithium batteries, with excellent electrical insulation performance and thermal stability.
Packaging industry: producing high barrier film, widely used in packaging of food, cosmetics, etc., to extend the shelf life and service life of products.
Photovoltaic industry: used for producing encapsulation films in photovoltaic modules to protect solar cells from external environmental influences.
4. Advantages
The significant advantages of membrane casting and stretching equipment are:
Efficient production: The equipment design ensures a continuous production process and enables the rapid production of high-quality films.
Excellent product performance: Through the stretching process, the physical, mechanical, and barrier properties of the film are significantly improved.
Strong adaptability: Adjustable process parameters enable the equipment to adapt to different types and characteristics of polymers, meeting diverse market demands.
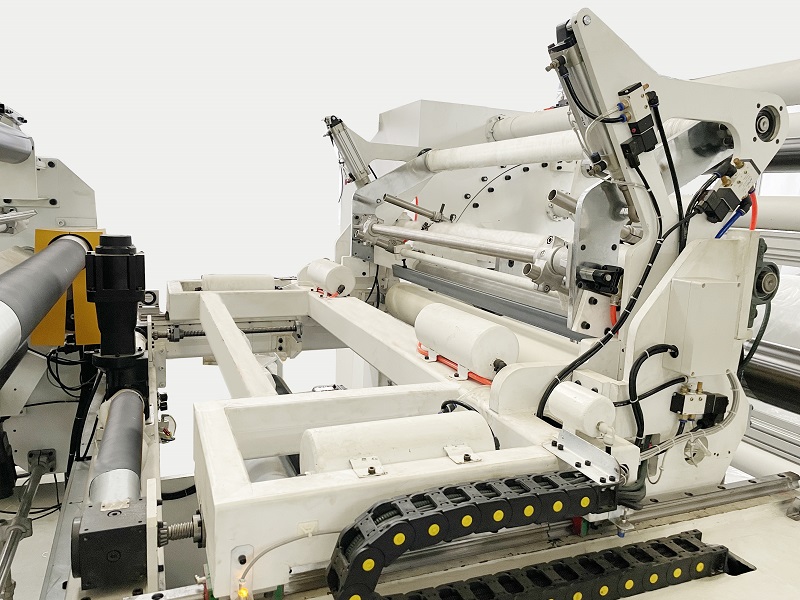
The diaphragm casting and stretching equipment mainly consists of the following parts:
Extruder: Heat and melt plastic resin, and extrude it into a film through a screw. This section is usually equipped with a temperature control system to ensure the stability of the molten state.
Casting mold: used to rapidly solidify molten plastic into thin films, its design directly affects the thickness and uniformity of the film. Molds generally use cooling systems to accelerate the cooling and solidification process of molten plastics.
Cooling device: By means of air cooling or water cooling, the initially formed film is rapidly cooled to maintain its shape and performance.
Stretching device: including a longitudinal stretching machine and a transverse stretching machine, which apply tensile force to the film to change its physical and chemical properties. The stretching process can improve the mechanical strength and barrier properties of the film.
Winding equipment: Roll the stretched film into a roll for subsequent processing and transportation.
In the membrane casting and stretching equipment, firstly, the polymer raw material is melted and uniformly stirred by an extruder, and then passed through a casting mold to form a preliminary film. After cooling, the film is transported to a stretching device for longitudinal and transverse stretching. The stretching process can effectively rearrange the molecular chains, thereby improving the strength, transparency, and durability of the film.
The production of thin films by membrane casting and stretching equipment is suitable for multiple industries:
Electronics industry: Used for manufacturing separators for polymer lithium batteries, with excellent electrical insulation performance and thermal stability.
Packaging industry: producing high barrier film, widely used in packaging of food, cosmetics, etc., to extend the shelf life and service life of products.
Photovoltaic industry: used for producing encapsulation films in photovoltaic modules to protect solar cells from external environmental influences.
4. Advantages
The significant advantages of membrane casting and stretching equipment are:
Efficient production: The equipment design ensures a continuous production process and enables the rapid production of high-quality films.
Excellent product performance: Through the stretching process, the physical, mechanical, and barrier properties of the film are significantly improved.
Strong adaptability: Adjustable process parameters enable the equipment to adapt to different types and characteristics of polymers, meeting diverse market demands.
Author:admin