What are the requirements for the raw materials used in the plastic hollow board production line
DATE:2024/9/26 10:54:30 / READ: / SOURCE:This station
Plastic hollow board is a widely used new type of board, most commonly used in fields such as packaging, construction, advertising, etc. At present, the main raw materials used in the production of plastic hollow boards are polymers, such as polypropylene (PP), polyethylene (PE), etc. During the operation of the plastic hollow board production line, in order to ensure the production quality of the hollow board and the stability of the equipment, special care must be taken when selecting raw materials. Only materials that meet the following characteristics can be put into use.
Melt Flow Index (MFI): MFI is an important indicator for measuring the flowability of materials in a heated state. For polypropylene and polyethylene, their MFI values need to be within a certain range to ensure smooth flow during extrusion. Appropriate melt flowability helps with molding, reducing machine jamming and other issues during the production process.
Density: The density of the material directly affects the strength and weight of the hollow board. Usually, the density of polypropylene is between 0.90-0.92g/cm ³, while the density of polyethylene is relatively low, around 0.91-0.96g/cm ³. Choosing the appropriate density can ensure that the hollow board has ideal mechanical properties and economy.
2. Mechanical properties
Tensile strength and compressive strength: Plastic hollow boards are often used for transportation packaging or as building materials, so they are required to have certain tensile strength and compressive strength. The selection of raw materials should have good mechanical properties to meet the requirements of external pressure and impact.
Flexibility and resilience: Flexibility refers to the ability of a material to bend under external forces without easily breaking, while resilience refers to the ability of a material to absorb energy without easily breaking. The raw materials for producing hollow boards must have appropriate flexibility and toughness to improve the durability and service life of the product.
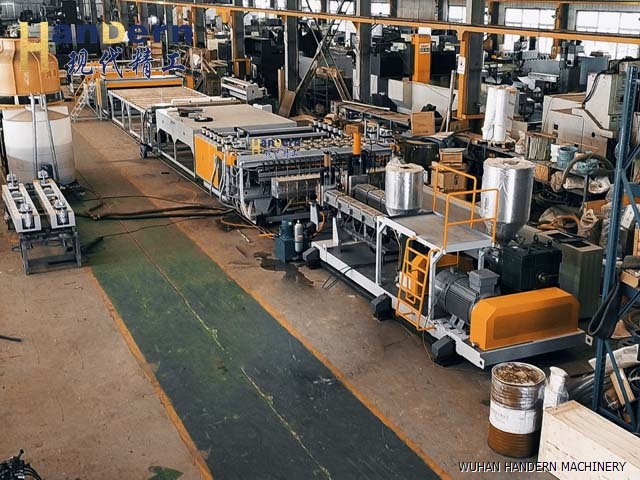
UV resistance: Hollow boards are often used for outdoor applications, so the raw materials should have good UV resistance to prevent degradation, fading, and brittleness under prolonged sunlight. Adding anti UV additives can enhance this characteristic.
Chemical resistance: Plastic hollow boards may come into contact with various chemicals, so the raw materials must have good chemical resistance and be able to resist corrosion from common acids, alkalis, and solvents.
4. Environmental friendliness
Recyclability: Under modern environmental requirements, plastic raw materials need to have good recyclability. The use of recyclable polypropylene or polyethylene materials can improve product environmental friendliness while reducing production costs.
Low volatile organic compounds (VOCs): During the production process, the release of volatile organic compounds from raw materials should be minimized as much as possible to reduce harm to the environment and operators.
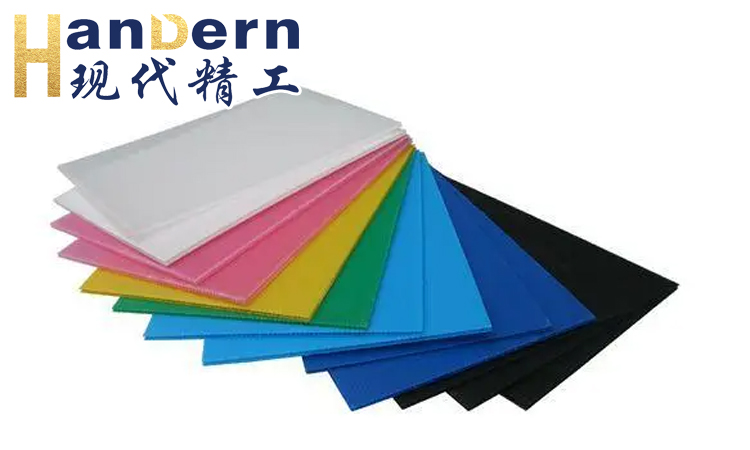
Processing temperature: The raw materials should have a suitable melting processing temperature. Excessive or insufficient melting temperature can affect the forming quality and various properties of the sheet metal. Optimized processing temperature helps improve production efficiency and finished product quality.
Author:admin