What is the appropriate operating speed control for the plastic hollow board production line
DATE:2024/8/29 14:36:26 / READ: / SOURCE:This station
The production process of plastic hollow boards involves multiple equipment and complex technological processes, among which the operating speed of the entire production line is an important factor affecting production efficiency and product quality. The following is a detailed analysis of the operating speed of the plastic hollow board production line.
1. Types and characteristics of production equipment
The production of hollow boards mainly relies on extruders (single screw or twin-screw) and corresponding downstream equipment, such as molds, cooling systems, and cutting equipment. The design and performance of different devices will directly affect their optimal operating speed.
Single screw extruder: usually suitable for medium to low speed operation, with a common operating speed range of 150-300 kg/h (depending on equipment specifications and production requirements).
Twin screw extruder: Due to its superior mixing and plasticizing capabilities, twin screw extruders can operate at higher speeds, commonly ranging from 300-450 kg/h, but also depending on the materials and product complexity used.
2. Factors affecting operating speed
Choosing the appropriate operating speed also requires consideration of the following factors:
Material properties: Different types of plastics (such as PP, PE, PC, etc.) have different flowability and melting temperatures, which affect their behavior during extrusion. Generally speaking, materials with good fluidity can increase their operating speed appropriately, while materials with poor fluidity should reduce their speed to ensure sufficient plasticization.
Product requirements: When manufacturing hollow boards, the thickness, density, and structure of the board directly affect the required operating speed. Thick plates usually require slower speeds during production to ensure uniformity and quality, while thin plates can be produced at higher speeds.
Mold design: The design of the mold (such as channel length, channel width, etc.) will affect the flow of molten material, thereby affecting the optimal operating speed. Reasonably designed molds can maintain good product quality at high speeds.
3. Balance between quality and efficiency
The choice of operating speed requires finding a balance between quality and efficiency. If the speed is too fast, although it can increase production, it may lead to uneven product, appearance defects, and decreased physical properties. However, if the running speed is too slow, although it can improve product quality, it will affect overall production efficiency and increase the cost per unit of product. Therefore, timely adjustments need to be made according to the production situation.
4. Monitoring and adjustment
Real time monitoring of the operation status and product quality of the plastic hollow board production line is crucial in the production process. If fluctuations in product quality are found, it is necessary to promptly check whether the equipment operating speed is appropriate and make adjustments if necessary. By making reasonable adjustments, production efficiency can be maximized while ensuring product quality.
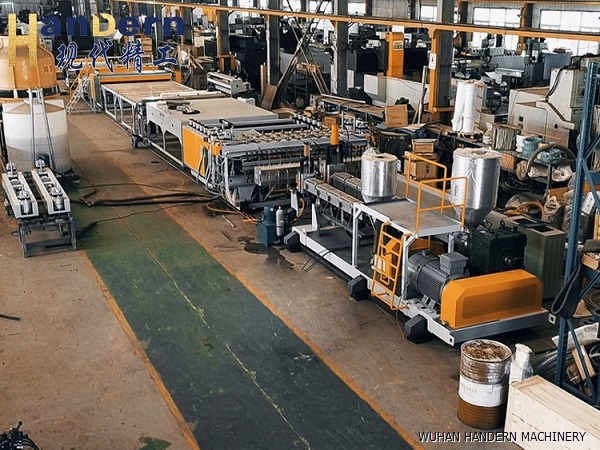
The production of hollow boards mainly relies on extruders (single screw or twin-screw) and corresponding downstream equipment, such as molds, cooling systems, and cutting equipment. The design and performance of different devices will directly affect their optimal operating speed.
Single screw extruder: usually suitable for medium to low speed operation, with a common operating speed range of 150-300 kg/h (depending on equipment specifications and production requirements).
Twin screw extruder: Due to its superior mixing and plasticizing capabilities, twin screw extruders can operate at higher speeds, commonly ranging from 300-450 kg/h, but also depending on the materials and product complexity used.
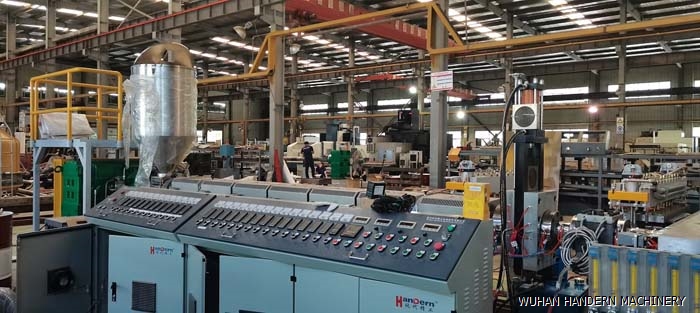
Choosing the appropriate operating speed also requires consideration of the following factors:
Material properties: Different types of plastics (such as PP, PE, PC, etc.) have different flowability and melting temperatures, which affect their behavior during extrusion. Generally speaking, materials with good fluidity can increase their operating speed appropriately, while materials with poor fluidity should reduce their speed to ensure sufficient plasticization.
Product requirements: When manufacturing hollow boards, the thickness, density, and structure of the board directly affect the required operating speed. Thick plates usually require slower speeds during production to ensure uniformity and quality, while thin plates can be produced at higher speeds.
Mold design: The design of the mold (such as channel length, channel width, etc.) will affect the flow of molten material, thereby affecting the optimal operating speed. Reasonably designed molds can maintain good product quality at high speeds.
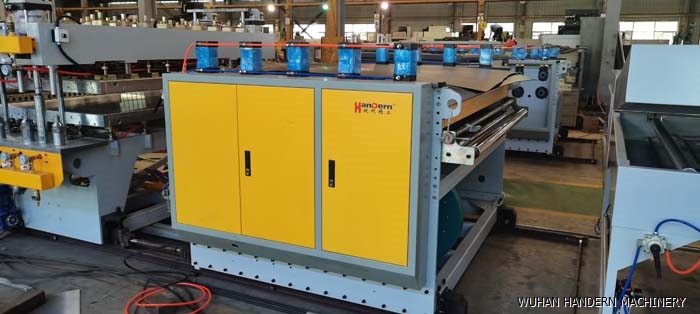
The choice of operating speed requires finding a balance between quality and efficiency. If the speed is too fast, although it can increase production, it may lead to uneven product, appearance defects, and decreased physical properties. However, if the running speed is too slow, although it can improve product quality, it will affect overall production efficiency and increase the cost per unit of product. Therefore, timely adjustments need to be made according to the production situation.
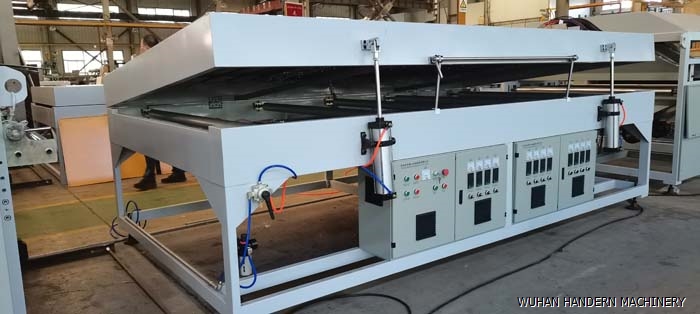
Real time monitoring of the operation status and product quality of the plastic hollow board production line is crucial in the production process. If fluctuations in product quality are found, it is necessary to promptly check whether the equipment operating speed is appropriate and make adjustments if necessary. By making reasonable adjustments, production efficiency can be maximized while ensuring product quality.
Author:admin