What are the common faults of plastic hollow grid board production line
DATE:2024/8/28 15:02:07 / READ: / SOURCE:This station
In actual production, the plastic hollow grid board production line may encounter various faults, which not only affect product quality, but also may lead to production stagnation and increase production costs. The following are some common faults and their possible causes and solutions for plastic hollow grid board production lines:
1. Equipment malfunction
Motor malfunction: The motor is the core power source of the production line, and if a malfunction occurs, it may cause the production line to stall. The common causes of motor failures include overload, overheating, and power supply issues. To solve this problem, it is necessary to regularly check the operating status of the motor, ensure that the load is within the rated range, and perform necessary cleaning and maintenance.
Temperature control system malfunction: If there is a problem with the temperature controller, it may cause uneven melting of the material, affecting the quality of the finished product. The causes of temperature control system failures may include sensor malfunctions, abnormal control programs, etc. Regular calibration and maintenance of temperature control equipment can effectively reduce the occurrence of such malfunctions.
2. Material issues
Raw material blockage: Using unqualified raw materials or granular materials with high impurities can cause blockages in the extruder's rubber discharge port, mold, and other parts, thereby affecting normal production. The solution includes strict inspection of raw materials, using high-quality materials such as polypropylene and polyethylene, and regularly cleaning the interior of the machine.
Humidity issue: After plastic particles absorb moisture, it will affect their melt flowability, which can easily lead to problems such as spring deviation and bubbles during the production process. It is recommended to dry the raw materials before production to reduce humidity.
3. Improper setting of production parameters
Unstable extrusion pressure: Improper extrusion pressure can directly affect the thickness and quality of the sheet. Possible reasons include poor fluidity of raw materials, insufficient feeding, etc. To solve this problem, it is necessary to adjust the temperature and speed of the extruder, as well as ensure uniform supply of materials.
Cooling system issue: Insufficient cooling may result in insufficient hardness of the plastic hollow board, affecting the peeling and surface quality of the finished product. If the cooling water flow is insufficient or the temperature is not suitable, it will affect the cooling effect. Regularly check the operation status of the cooling system and ensure the quality of the cooling water.
4. Mold related issues
Mold blockage: causing defective products on the production line, common reasons include mixed materials and excessive accumulation of materials. Regular cleaning of molds, use of appropriate materials, and maintenance and upkeep of molds can effectively prevent such problems.
Mold wear: With the extension of production time, molds will experience wear and tear, resulting in product dimensions not meeting standards. Regularly inspect the wear of molds and replace or repair them as needed to ensure stable quality of finished products.
5. Improper operation
Insufficient operator training: Sometimes operators have insufficient understanding of the equipment, leading to incorrect operations. Setting incorrect production parameters or neglecting equipment maintenance. Enterprises need to provide regular training for operators to enhance their professional skills and safety awareness.
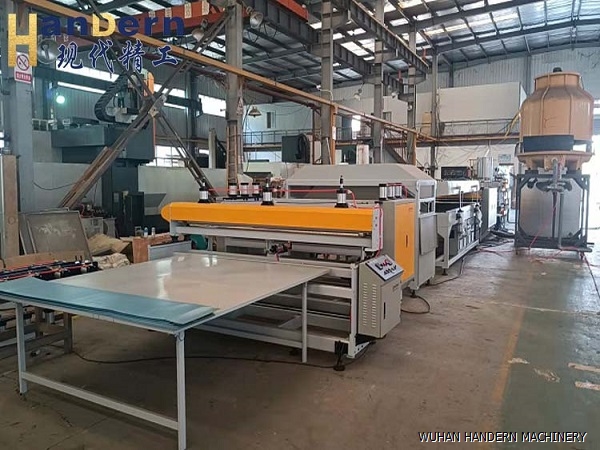
Motor malfunction: The motor is the core power source of the production line, and if a malfunction occurs, it may cause the production line to stall. The common causes of motor failures include overload, overheating, and power supply issues. To solve this problem, it is necessary to regularly check the operating status of the motor, ensure that the load is within the rated range, and perform necessary cleaning and maintenance.
Temperature control system malfunction: If there is a problem with the temperature controller, it may cause uneven melting of the material, affecting the quality of the finished product. The causes of temperature control system failures may include sensor malfunctions, abnormal control programs, etc. Regular calibration and maintenance of temperature control equipment can effectively reduce the occurrence of such malfunctions.
2. Material issues
Raw material blockage: Using unqualified raw materials or granular materials with high impurities can cause blockages in the extruder's rubber discharge port, mold, and other parts, thereby affecting normal production. The solution includes strict inspection of raw materials, using high-quality materials such as polypropylene and polyethylene, and regularly cleaning the interior of the machine.
Humidity issue: After plastic particles absorb moisture, it will affect their melt flowability, which can easily lead to problems such as spring deviation and bubbles during the production process. It is recommended to dry the raw materials before production to reduce humidity.
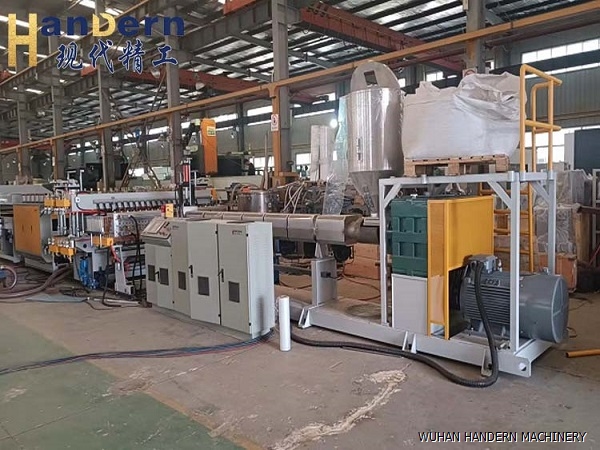
Unstable extrusion pressure: Improper extrusion pressure can directly affect the thickness and quality of the sheet. Possible reasons include poor fluidity of raw materials, insufficient feeding, etc. To solve this problem, it is necessary to adjust the temperature and speed of the extruder, as well as ensure uniform supply of materials.
Cooling system issue: Insufficient cooling may result in insufficient hardness of the plastic hollow board, affecting the peeling and surface quality of the finished product. If the cooling water flow is insufficient or the temperature is not suitable, it will affect the cooling effect. Regularly check the operation status of the cooling system and ensure the quality of the cooling water.
4. Mold related issues
Mold blockage: causing defective products on the production line, common reasons include mixed materials and excessive accumulation of materials. Regular cleaning of molds, use of appropriate materials, and maintenance and upkeep of molds can effectively prevent such problems.
Mold wear: With the extension of production time, molds will experience wear and tear, resulting in product dimensions not meeting standards. Regularly inspect the wear of molds and replace or repair them as needed to ensure stable quality of finished products.
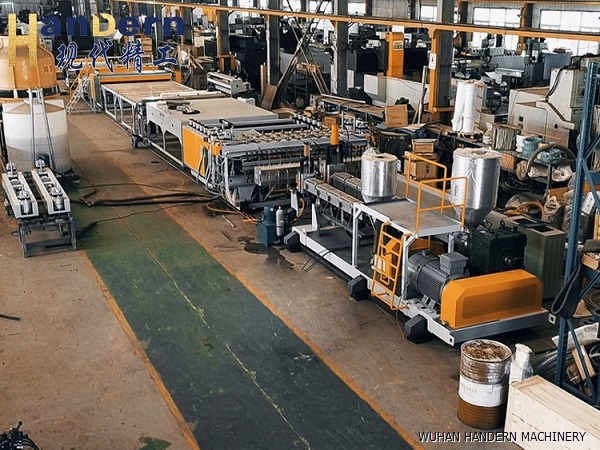
Insufficient operator training: Sometimes operators have insufficient understanding of the equipment, leading to incorrect operations. Setting incorrect production parameters or neglecting equipment maintenance. Enterprises need to provide regular training for operators to enhance their professional skills and safety awareness.
Author:admin