What should be noted in the normal operation of equipment for producing hollow panels
DATE:2024/6/29 14:13:43 / READ: / SOURCE:This station
The equipment for making hollow panels is a complete production line assembled from a series of mechanical equipment. If we want this production line to run smoothly, we need to set up these components from multiple aspects in a reasonable manner. So, what specific aspects do we need to pay special attention to? Wuhan Modern Precision Machinery Co., Ltd. is very familiar with equipment for producing hollow panels. We have over 30 years of experience in researching, producing, and selling such production lines. Now, let me explain in detail how we should set up and coordinate this entire production line.
Raw material control: The processing of raw materials is the most fundamental aspect of ensuring the smooth operation of the entire production line. We need to accurately control the proportion and feeding speed of raw materials to ensure that the extruder can stably and uniformly extrude plastic materials and ensure the quality of product molding.
Temperature control: The extruder and mold should be set with appropriate extrusion and mold temperatures based on the specific plastic material being produced. Different plastic materials have different temperature requirements, and an appropriate temperature can ensure extrusion and molding effects, while avoiding deformation of plastic materials.
Speed control: The control of operating speed is crucial as it affects almost all components of the entire production line. When designing the operating speed, we need to consider extrusion efficiency, forming efficiency, drying efficiency, and cooling efficiency. Only after considering all of these factors can we set an appropriate operating speed. If it is too fast, it will cause product deformation, and if it is too slow, it will affect production efficiency.
Pressure control: It is necessary to set appropriate extruder pressure and mold pressure according to the characteristics of different plastic materials and the size requirements of the product. Excessive pressure may lead to excessive equipment load, while insufficient pressure may affect the extrusion effect and quality of the product.
Cooling control: The cooling effect of the cooling machine has a significant impact on the quality of the formed product. Appropriate cooling time and temperature should be set according to factors such as the melting point of plastic materials and the size of the product to ensure the quality of the product after cooling and forming.
By controlling these settings well, we can basically ensure that the equipment for producing hollow panels can operate in a balanced manner. However, in addition, we also remind everyone to pay attention to the maintenance and upkeep of the entire production line, which is also very important.
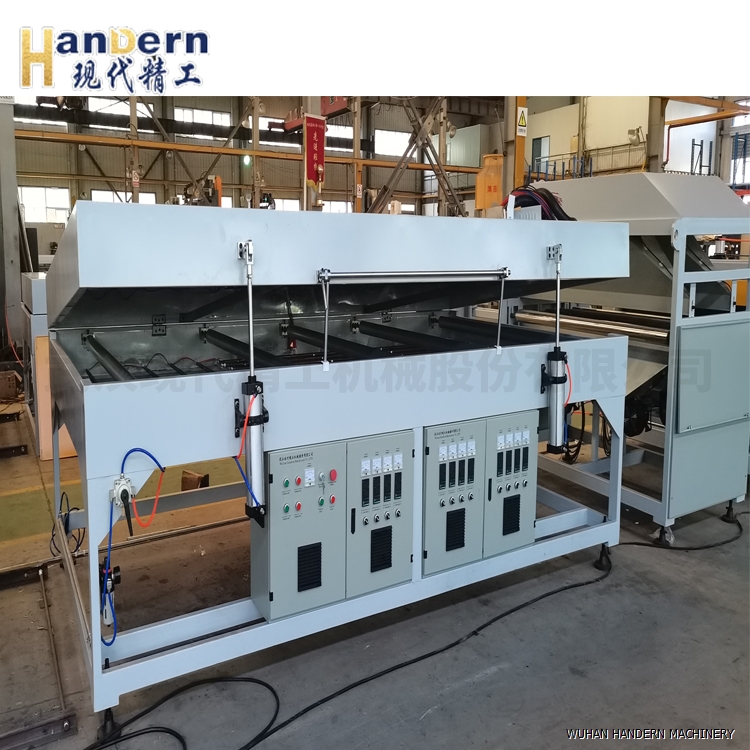
Temperature control: The extruder and mold should be set with appropriate extrusion and mold temperatures based on the specific plastic material being produced. Different plastic materials have different temperature requirements, and an appropriate temperature can ensure extrusion and molding effects, while avoiding deformation of plastic materials.
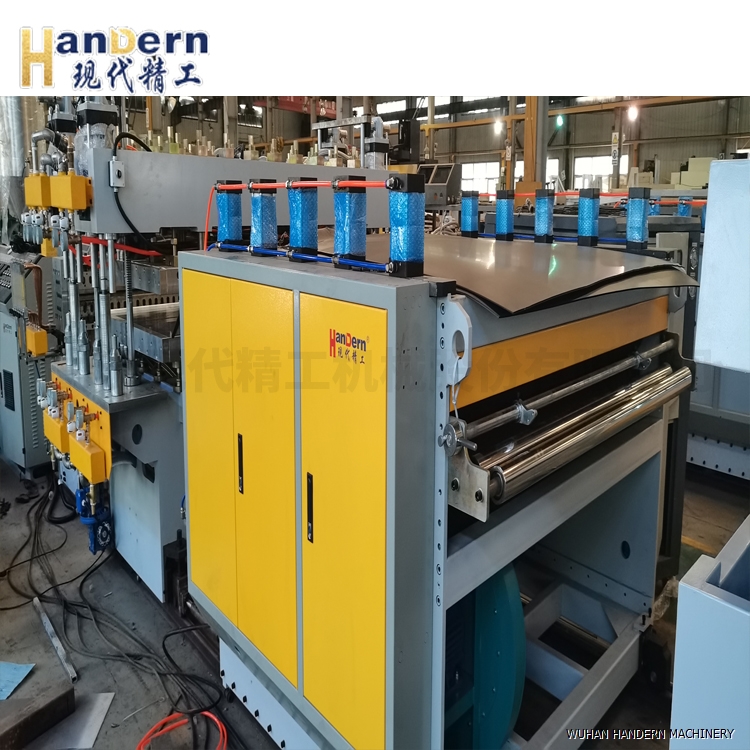
Pressure control: It is necessary to set appropriate extruder pressure and mold pressure according to the characteristics of different plastic materials and the size requirements of the product. Excessive pressure may lead to excessive equipment load, while insufficient pressure may affect the extrusion effect and quality of the product.
Cooling control: The cooling effect of the cooling machine has a significant impact on the quality of the formed product. Appropriate cooling time and temperature should be set according to factors such as the melting point of plastic materials and the size of the product to ensure the quality of the product after cooling and forming.
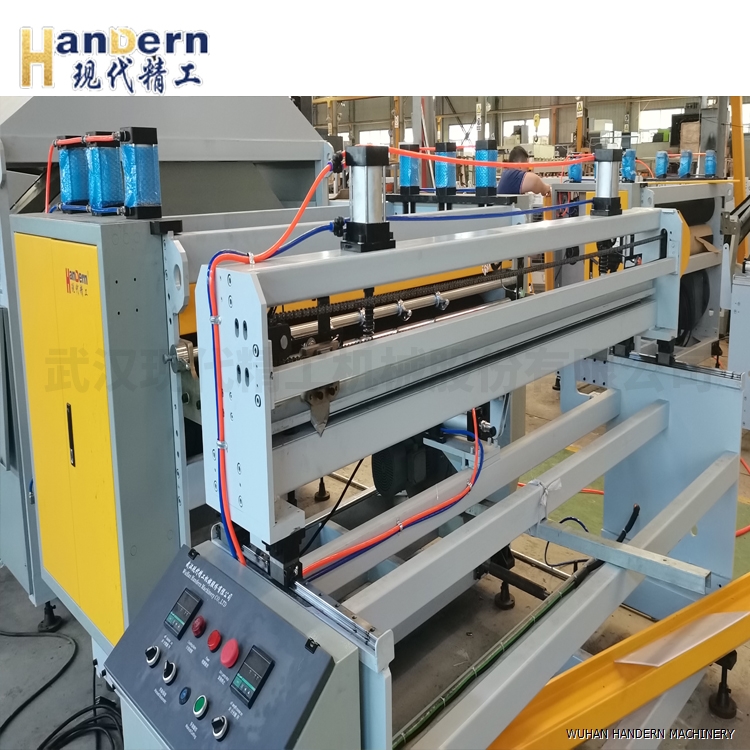
Author:admin