What are the working principles and difficulties of the film laminating machine
DATE:2023/7/7 14:34:36 / READ: / SOURCE:This station
The laminating machine can be widely used in various industries, among which the most common applications are plastic packaging, paper plastic packaging, various paper cup packaging, and other industries. The process of film coating composite machine is complex and difficult, and its workflow usually includes the following steps:
1. Preparation of substrate: Cut, clean, and dry the substrate to be coated to ensure a clean and flat surface.
2. Coating: Apply the coating solution evenly onto the surface of the substrate through the coating head, forming a thin film. The coating solution can be coatings, adhesives, or other coating materials.
3. Drying: The substrate after coating is sent to a drying chamber for drying to remove solvents or moisture from the coating solution and form a solid film.
4. Composite: Composite the coated substrate with another layer of material (such as paper, film, etc.) to form a coated composite material.
5. Sorting: Organize and cut the composite material to meet the required size and shape.
In the above workflow, the technical difficulties of the film coating composite machine mainly include the following aspects:
1. Uniformity of coating: The uniform coating of coating solution is a key factor in ensuring the quality of coating. The viscosity, fluidity, and design and adjustment of the coating head of the coating solution will all affect the uniformity of the coating. Ensure that the coating solution can evenly cover the entire substrate surface to avoid uneven thickness of the coating solution.
2. Drying control: The coating solution needs to be dried after coating to form a solid film. The control of drying parameters such as temperature, time, and humidity is very important, as high or low temperature and humidity can affect the quality of the film. At the same time, different coating solutions also require different drying processes to ensure coating quality.
3. Composite bonding: The coating and laminating machine needs to ensure strong bonding between the coating layer and another layer of material (such as paper, film, etc.). The technical difficulties of composite bonding lie in the selection and use of adhesives, as well as the control of composite pressure and temperature. The composite of different materials requires different adhesives and process parameters.
4. Equipment debugging and maintenance: The film laminating machine is a complex equipment that requires debugging and maintenance to ensure its normal operation and stability. The mechanical structure, electrical control system, and coordination of coating, drying, and composite parts of the equipment require precise debugging and maintenance. In addition, the cleaning and maintenance of equipment are also important steps to ensure the quality of the coating.
The common lamination methods for laminating machines include single sided lamination and double sided lamination, and their difference lies in the position of the lamination. Single sided coating is only applied on one side of the substrate, while double sided coating is applied on both sides of the substrate. Single sided coating is commonly used to make materials for single sided coatings, such as billboards, logos, etc. Double sided coating is often used to make materials for double-sided coatings, such as packaging materials, protective films, etc.
If you would like to learn more about film laminating machines, please feel free to consult us at any time or visit the manufacturer for inspection.
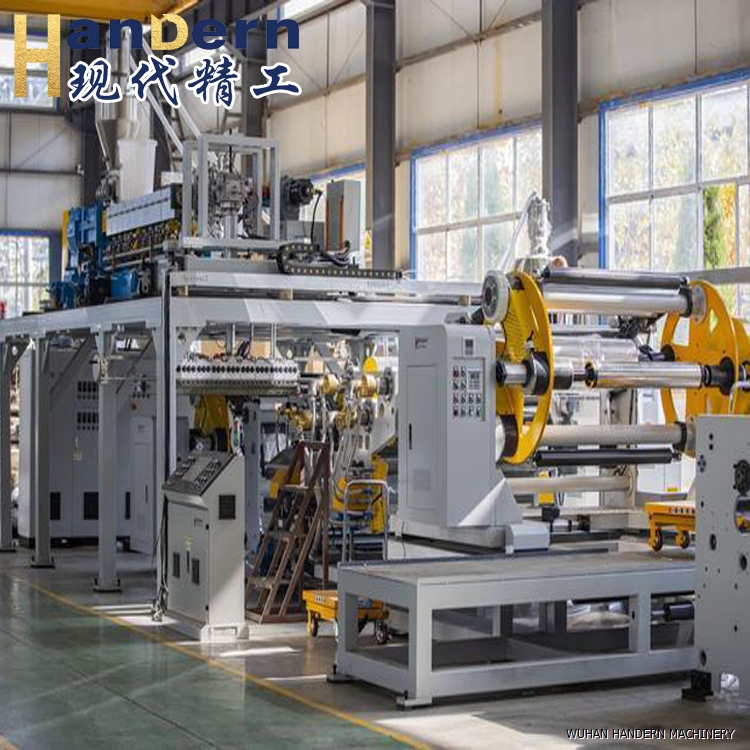
2. Coating: Apply the coating solution evenly onto the surface of the substrate through the coating head, forming a thin film. The coating solution can be coatings, adhesives, or other coating materials.
3. Drying: The substrate after coating is sent to a drying chamber for drying to remove solvents or moisture from the coating solution and form a solid film.
4. Composite: Composite the coated substrate with another layer of material (such as paper, film, etc.) to form a coated composite material.
5. Sorting: Organize and cut the composite material to meet the required size and shape.
In the above workflow, the technical difficulties of the film coating composite machine mainly include the following aspects:
1. Uniformity of coating: The uniform coating of coating solution is a key factor in ensuring the quality of coating. The viscosity, fluidity, and design and adjustment of the coating head of the coating solution will all affect the uniformity of the coating. Ensure that the coating solution can evenly cover the entire substrate surface to avoid uneven thickness of the coating solution.
2. Drying control: The coating solution needs to be dried after coating to form a solid film. The control of drying parameters such as temperature, time, and humidity is very important, as high or low temperature and humidity can affect the quality of the film. At the same time, different coating solutions also require different drying processes to ensure coating quality.
3. Composite bonding: The coating and laminating machine needs to ensure strong bonding between the coating layer and another layer of material (such as paper, film, etc.). The technical difficulties of composite bonding lie in the selection and use of adhesives, as well as the control of composite pressure and temperature. The composite of different materials requires different adhesives and process parameters.
4. Equipment debugging and maintenance: The film laminating machine is a complex equipment that requires debugging and maintenance to ensure its normal operation and stability. The mechanical structure, electrical control system, and coordination of coating, drying, and composite parts of the equipment require precise debugging and maintenance. In addition, the cleaning and maintenance of equipment are also important steps to ensure the quality of the coating.
The common lamination methods for laminating machines include single sided lamination and double sided lamination, and their difference lies in the position of the lamination. Single sided coating is only applied on one side of the substrate, while double sided coating is applied on both sides of the substrate. Single sided coating is commonly used to make materials for single sided coatings, such as billboards, logos, etc. Double sided coating is often used to make materials for double-sided coatings, such as packaging materials, protective films, etc.
If you would like to learn more about film laminating machines, please feel free to consult us at any time or visit the manufacturer for inspection.
Author:admin