The PP plastic hollow board production line is assembled from these components
DATE:2023/6/8 14:34:40 / READ: / SOURCE:This station
The PP plastic hollow board production line produces a new type of lightweight and environmentally friendly material, which is widely used in advertising, packaging, partition, sound insulation, waterproofing and other fields. Compared with traditional plastic and paper products, it has better performance, longer service life, and can be recycled multiple times. Today, I would like to introduce in detail the components of the PP plastic hollow board production line and the functions of each component.
The entire production line mainly consists of the following parts: raw material pretreatment system, plastic extruder, mold, cooling system, cutting system, winding system, etc.
The first is the raw material pretreatment system. The production line of PP plastic hollow board requires the use of PP raw materials, fillers, stabilizers, etc. Therefore, it is necessary to pre-treat these raw materials. Pre processing includes steps such as mixing, drying, and screening of raw materials to ensure the quality and stability of the raw materials.
Next is the plastic extruder. The plastic extruder is the core part of the PP plastic hollow board production line. It feeds the pre processed raw materials into the heating cylinder of the extruder, and under heating and pressure, the plastic is extruded into a hollow plate shape. The technical level of the extruder has a crucial impact on the quality and production efficiency of the product.
The mold is also an indispensable part of the PP plastic hollow board production line. The design and manufacturing of molds directly affect the appearance, size, quality, and other aspects of products. There are various types of molds, and different molds can be designed according to different needs to meet market demands.
The cooling system is designed to quickly cool the extruded hollow plate to ensure its stability in shape and size. The cooling system generally adopts two methods: air cooling and water cooling, which can be selected according to different production needs.
The cutting system is to cut the extruded hollow board according to a certain size and can perform different shapes of cutting. The design and operation of the cutting system directly affect the dimensional accuracy and appearance quality of the product.
The winding system collects the cut hollow plates for subsequent packaging and transportation. The design of the winding system should consider the size and weight of the product to ensure production efficiency and product quality.
In short, the PP plastic hollow board production line is a complex system engineering that requires the collaborative cooperation of various parts to ensure product quality and production efficiency. With the continuous development and innovation of technology, the PP plastic hollow board production line is also constantly updated and improved, bringing more high-quality and environmentally friendly products to the market.
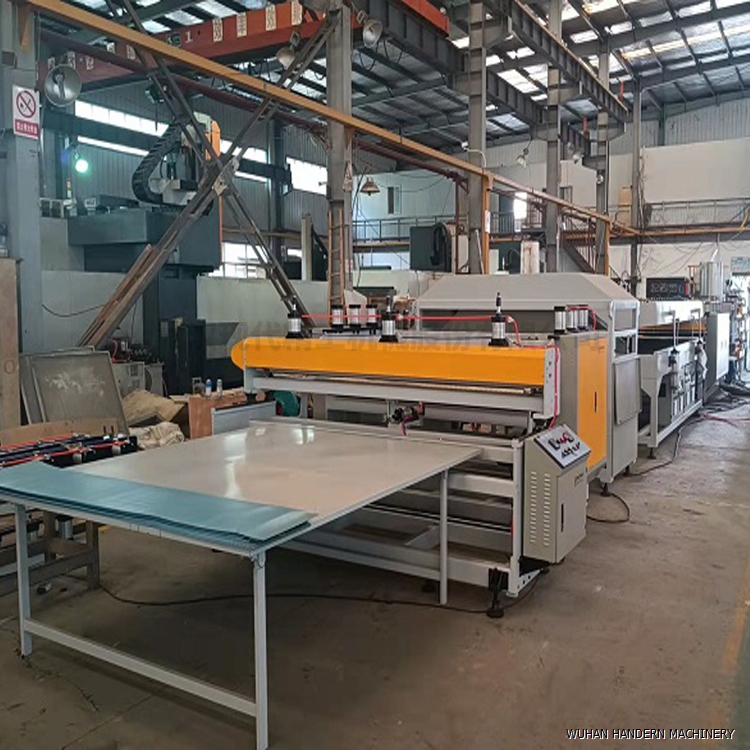
The first is the raw material pretreatment system. The production line of PP plastic hollow board requires the use of PP raw materials, fillers, stabilizers, etc. Therefore, it is necessary to pre-treat these raw materials. Pre processing includes steps such as mixing, drying, and screening of raw materials to ensure the quality and stability of the raw materials.
Next is the plastic extruder. The plastic extruder is the core part of the PP plastic hollow board production line. It feeds the pre processed raw materials into the heating cylinder of the extruder, and under heating and pressure, the plastic is extruded into a hollow plate shape. The technical level of the extruder has a crucial impact on the quality and production efficiency of the product.
The mold is also an indispensable part of the PP plastic hollow board production line. The design and manufacturing of molds directly affect the appearance, size, quality, and other aspects of products. There are various types of molds, and different molds can be designed according to different needs to meet market demands.
The cooling system is designed to quickly cool the extruded hollow plate to ensure its stability in shape and size. The cooling system generally adopts two methods: air cooling and water cooling, which can be selected according to different production needs.
The cutting system is to cut the extruded hollow board according to a certain size and can perform different shapes of cutting. The design and operation of the cutting system directly affect the dimensional accuracy and appearance quality of the product.
The winding system collects the cut hollow plates for subsequent packaging and transportation. The design of the winding system should consider the size and weight of the product to ensure production efficiency and product quality.
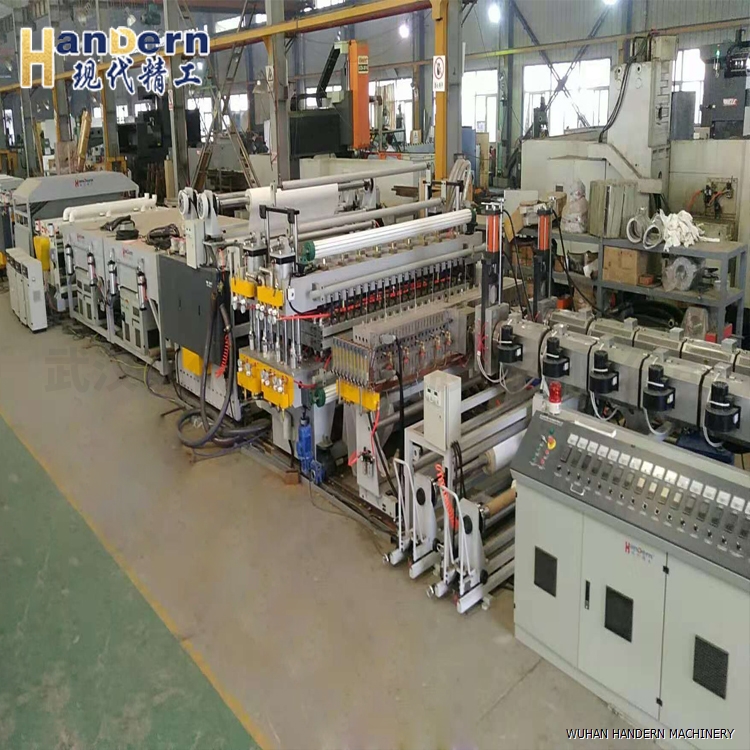
Author:admin