What is the reasonable setting for the screw speed of the hollow grid board production equipment
DATE:2024/12/30 11:00:49 / READ: / SOURCE:This station
Hollow grid board is a commonly used plastic product, widely used in packaging, construction, advertising and other fields. In the process of producing hollow grid panels, the screw speed of the equipment is an extremely important parameter, which has a significant impact on product quality, production efficiency, and equipment wear. Generally speaking, a reasonable screw speed can optimize the melting plasticization and mixing process, ensuring the production of hollow grid plates that meet the requirements.
1. Basic concept of screw speed
The screw speed refers to the number of revolutions per minute that the screw of the extruder rotates. The selection of rotational speed within a certain range will have a direct impact on the melting, mixing, transportation, and molding of plastics. Usually, the speed range of the screw varies from tens of revolutions per minute to hundreds of revolutions per minute, depending on the type of material used and production requirements.
2. Characteristics of materials
When choosing the appropriate screw speed, it is necessary to consider the type of material used. For example, the melt index, flowability, and thermal stability of polypropylene (PP) and polyethylene (PE) are different. Generally speaking, for materials with good fluidity, a higher screw speed (such as 80-150 revolutions per minute) can be chosen. For materials with poor fluidity, it is necessary to reduce the rotational speed (usually between 30-80 revolutions per minute) to ensure sufficient plasticization and prevent the material from remaining in the screw for too long and causing degradation.
3. Balance of production efficiency
The screw speed directly affects production efficiency. A higher rotational speed can increase production output, but excessive rotational speed may lead to high melting temperature, increase the risk of material degradation, and thus affect product quality. In addition, it may also lead to increased wear and tear of the equipment, shortening its service life. On the contrary, although low rotational speed can maintain good material quality, it will reduce production efficiency. Therefore, a balance needs to be struck between production efficiency and product quality.
4. Temperature control
The combination of screw speed and temperature is equally important. At high speeds, the residence time of the material inside the screw is relatively short, which can easily lead to incomplete plasticization. Therefore, when setting the screw speed, it is often necessary to increase the melt temperature accordingly to ensure good plasticizing effect. For example, at higher speeds of 500-600 revolutions per minute, it is usually necessary to set the temperature between 220-240 degrees Celsius to ensure the fluidity and plasticization quality of the material.
5. Screw design
The design of the screw also affects the appropriate rotational speed. The plasticizing effect of different designed screws on materials varies greatly at the same rotational speed. For example, screw designs with higher mixing capacity can achieve better mixing effects at low speeds, providing strong support for improving product quality. Therefore, choosing the appropriate screw design is an important factor in ensuring a reasonable rotational speed.
6. Setting of equipment production parameters
When setting the screw speed, it is recommended that the manufacturer refer to the equipment manual and the manufacturer's recommended parameters, and make appropriate adjustments and optimizations to the actual production process. According to production and market feedback, adjust the speed in a timely manner to ensure the stability and controllability of the product.
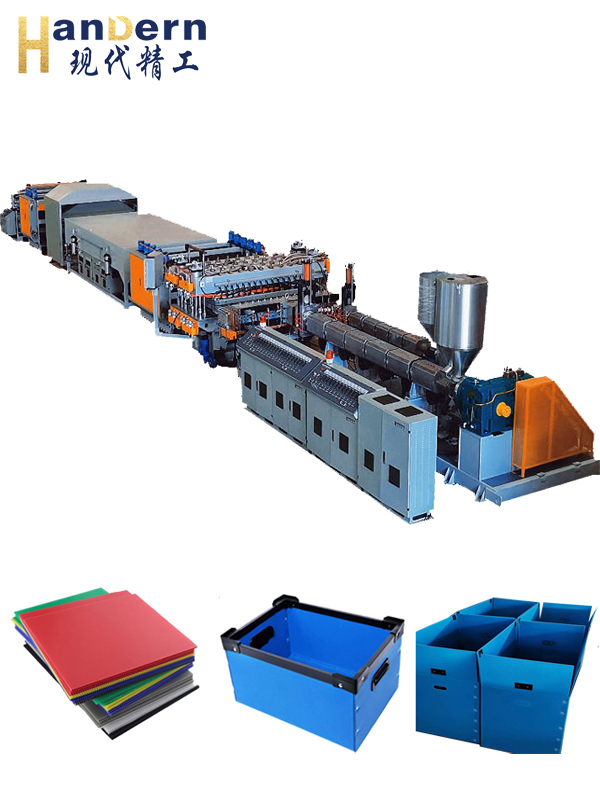
The screw speed refers to the number of revolutions per minute that the screw of the extruder rotates. The selection of rotational speed within a certain range will have a direct impact on the melting, mixing, transportation, and molding of plastics. Usually, the speed range of the screw varies from tens of revolutions per minute to hundreds of revolutions per minute, depending on the type of material used and production requirements.
2. Characteristics of materials
When choosing the appropriate screw speed, it is necessary to consider the type of material used. For example, the melt index, flowability, and thermal stability of polypropylene (PP) and polyethylene (PE) are different. Generally speaking, for materials with good fluidity, a higher screw speed (such as 80-150 revolutions per minute) can be chosen. For materials with poor fluidity, it is necessary to reduce the rotational speed (usually between 30-80 revolutions per minute) to ensure sufficient plasticization and prevent the material from remaining in the screw for too long and causing degradation.
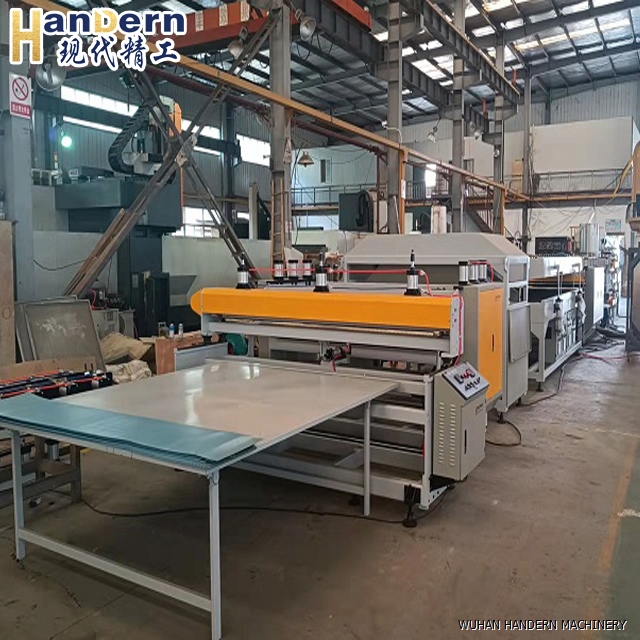
The screw speed directly affects production efficiency. A higher rotational speed can increase production output, but excessive rotational speed may lead to high melting temperature, increase the risk of material degradation, and thus affect product quality. In addition, it may also lead to increased wear and tear of the equipment, shortening its service life. On the contrary, although low rotational speed can maintain good material quality, it will reduce production efficiency. Therefore, a balance needs to be struck between production efficiency and product quality.
4. Temperature control
The combination of screw speed and temperature is equally important. At high speeds, the residence time of the material inside the screw is relatively short, which can easily lead to incomplete plasticization. Therefore, when setting the screw speed, it is often necessary to increase the melt temperature accordingly to ensure good plasticizing effect. For example, at higher speeds of 500-600 revolutions per minute, it is usually necessary to set the temperature between 220-240 degrees Celsius to ensure the fluidity and plasticization quality of the material.
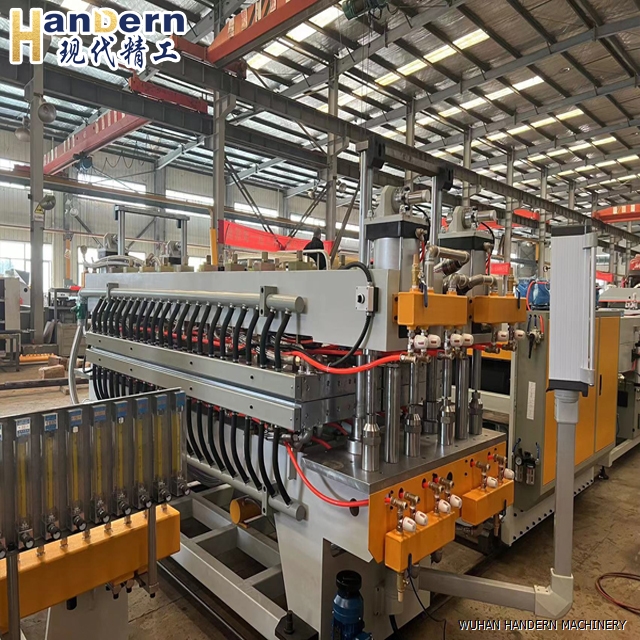
The design of the screw also affects the appropriate rotational speed. The plasticizing effect of different designed screws on materials varies greatly at the same rotational speed. For example, screw designs with higher mixing capacity can achieve better mixing effects at low speeds, providing strong support for improving product quality. Therefore, choosing the appropriate screw design is an important factor in ensuring a reasonable rotational speed.
6. Setting of equipment production parameters
When setting the screw speed, it is recommended that the manufacturer refer to the equipment manual and the manufacturer's recommended parameters, and make appropriate adjustments and optimizations to the actual production process. According to production and market feedback, adjust the speed in a timely manner to ensure the stability and controllability of the product.
Author:admin