How does the biaxially oriented film extrusion equipment work
DATE:2024/12/25 10:24:41 / READ: / SOURCE:This station
Biaxially oriented film extrusion equipment is a mechanical device used for producing high-performance films, widely used in fields such as food packaging, pharmaceutical packaging, and industrial films. Its working principle involves multiple steps, including extrusion, stretching, cooling, and winding. The following is a detailed analysis of the working process of the biaxially oriented film extrusion equipment.
1. Raw material preparation
Before the equipment starts working, the required raw materials are usually plastic pellets such as polyethylene (PE) and polypropylene (PP). These raw materials will be cleaned and dried before extrusion to ensure they are dry and free of impurities. Raw materials can also be supplemented with corresponding additives or pigments according to different production requirements.
2. Extrusion process
The raw material particles enter the extruder through the feeding device. The screw of the extruder rotates under the drive of the electric motor, and the frictional heat generated by the rotation of the screw heats the plastic particles to their melting temperature (usually 180 ° C to 230 ° C). The molten plastic forms the initial shape of a thin film through the mold head, usually a thin film tube.
3. Preliminary molding
The molten plastic output is formed into a hollow thin film tube through a circular die. At this point, the diameter and thickness of the thin film tube are usually determined by the flow rate of the mold head and molten plastic. The flushing pipe will be sent into the cooling area.
4. Bi directional stretching
Bi directional stretching is the core process of this equipment. After cooling, the thin film tube is stretched through a clamping system. This process can be divided into two directions of stretching: machine direction (MD) and transverse direction (TD).
Machine Direction Stretching (MD): The film tube is stretched in the longitudinal direction to increase its strength and rigidity.
Transverse Stretching (TD): After the film is cooled, the film tube is stretched in the transverse direction to further improve the physical properties of the film, enhance its tear resistance and transparency.
The stretching process is usually carried out at specific temperatures and stretching rates to ensure that the optical and mechanical properties of the film meet the expected standards.
5. Cooling and shaping
After stretching, the film is cooled by a cooling roller or water bath to fix it in its final shape and size. The cooling process rapidly reduces the temperature of the film, enhances its mechanical properties and dimensional stability, and avoids recycling and deformation.
6. Roll up
The cooled film is subjected to a trimming device to remove edge defects, and then wound into a roll by a winding machine. By adjusting the winding speed and tension, it is possible to ensure that the film is wound neatly and avoid wrinkles or folds.
7. Quality Inspection and Packaging
Finally, the wound film will undergo a series of quality inspections, including testing of thickness, transparency, strength, and other indicators. After passing the inspection, the film products will be packaged and ready to enter the market.
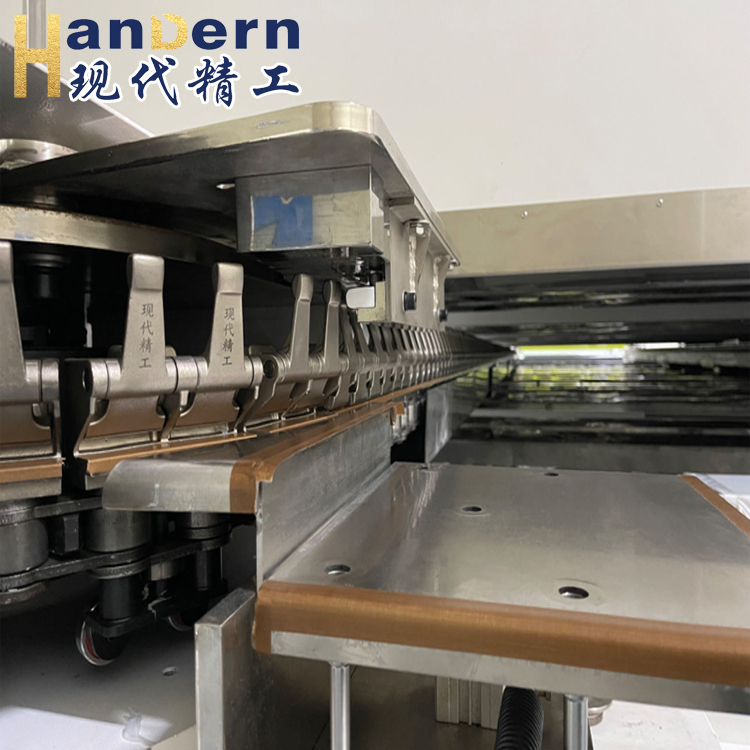
Before the equipment starts working, the required raw materials are usually plastic pellets such as polyethylene (PE) and polypropylene (PP). These raw materials will be cleaned and dried before extrusion to ensure they are dry and free of impurities. Raw materials can also be supplemented with corresponding additives or pigments according to different production requirements.
2. Extrusion process
The raw material particles enter the extruder through the feeding device. The screw of the extruder rotates under the drive of the electric motor, and the frictional heat generated by the rotation of the screw heats the plastic particles to their melting temperature (usually 180 ° C to 230 ° C). The molten plastic forms the initial shape of a thin film through the mold head, usually a thin film tube.
3. Preliminary molding
The molten plastic output is formed into a hollow thin film tube through a circular die. At this point, the diameter and thickness of the thin film tube are usually determined by the flow rate of the mold head and molten plastic. The flushing pipe will be sent into the cooling area.
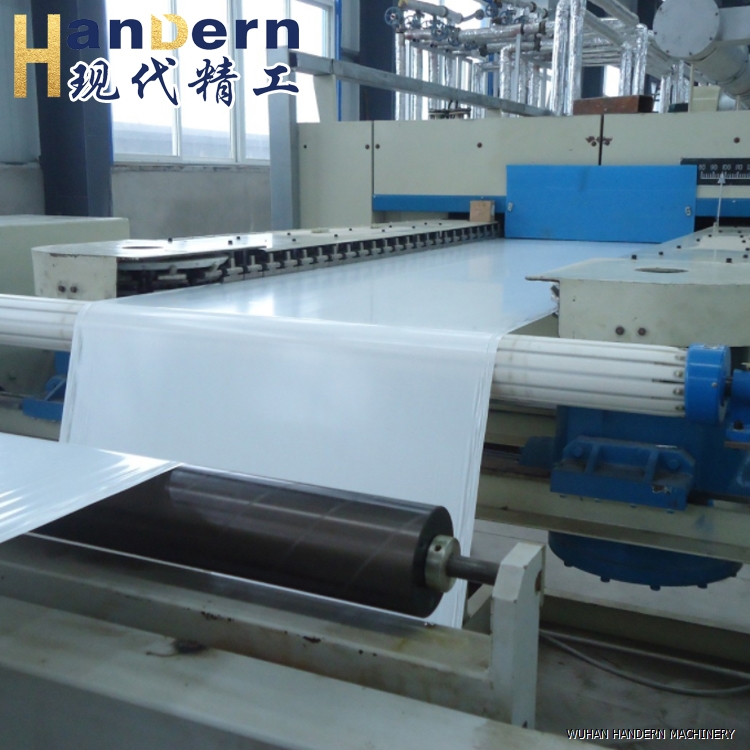
Bi directional stretching is the core process of this equipment. After cooling, the thin film tube is stretched through a clamping system. This process can be divided into two directions of stretching: machine direction (MD) and transverse direction (TD).
Machine Direction Stretching (MD): The film tube is stretched in the longitudinal direction to increase its strength and rigidity.
Transverse Stretching (TD): After the film is cooled, the film tube is stretched in the transverse direction to further improve the physical properties of the film, enhance its tear resistance and transparency.
The stretching process is usually carried out at specific temperatures and stretching rates to ensure that the optical and mechanical properties of the film meet the expected standards.
5. Cooling and shaping
After stretching, the film is cooled by a cooling roller or water bath to fix it in its final shape and size. The cooling process rapidly reduces the temperature of the film, enhances its mechanical properties and dimensional stability, and avoids recycling and deformation.
6. Roll up
The cooled film is subjected to a trimming device to remove edge defects, and then wound into a roll by a winding machine. By adjusting the winding speed and tension, it is possible to ensure that the film is wound neatly and avoid wrinkles or folds.
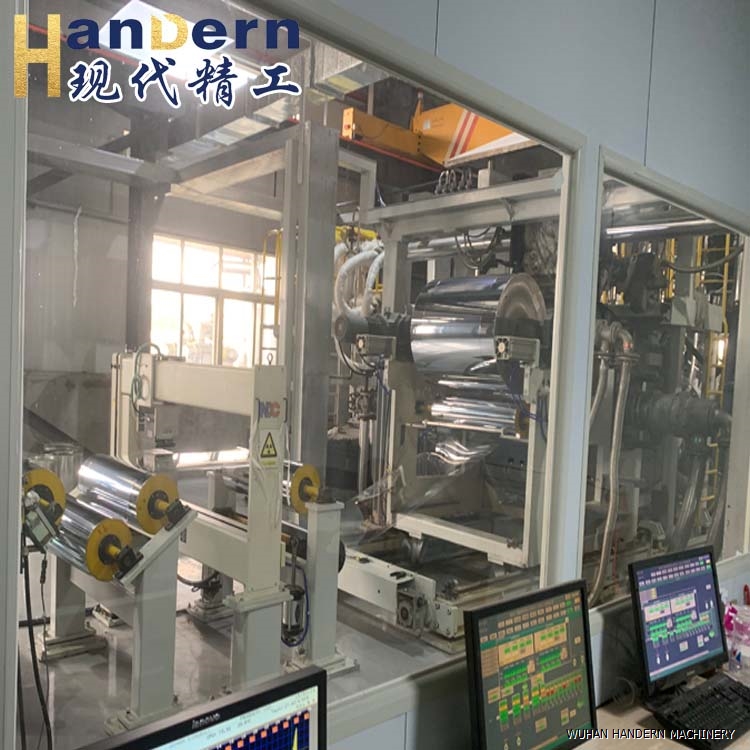
Finally, the wound film will undergo a series of quality inspections, including testing of thickness, transparency, strength, and other indicators. After passing the inspection, the film products will be packaged and ready to enter the market.
Author:admin