What are the most common problems encountered when starting a stone paper blown film paper machine
DATE:2024/12/13 9:41:42 / READ: / SOURCE:This station
The stone paper blown film paper machine may encounter some common problems when starting up, which often affect production efficiency and product quality. Here are some of the most commonly encountered problems and their possible causes:
1. Material issues
Raw material humidity: The main components of stone paper are calcium carbonate and resin. If the humidity of the raw material is high, it may cause problems during the film formation process, affecting the quality of the film.
Uneven mixing of raw materials: Improper proportioning or uneven mixing of raw materials for stone paper may lead to unstable properties of the molten material, thereby affecting the quality of the final film.
2. Equipment issues
Heating failure: If the heating device does not work properly before starting up, it may cause the raw materials to fail to reach the required melting temperature, affecting the extrusion process.
Blockage of extruder: If the equipment is not cleaned thoroughly or there are impurities in the raw materials after the last production, it may cause blockage of the extruder and affect the production process.
Mold malfunction: If the mold part is not installed correctly or damaged, it can cause uneven film thickness or defects.
3. Operational issues
Insufficient training for operators: If operators are not familiar with the operation process of the equipment, they may make operational errors, resulting in the equipment not being able to start normally.
Improper control system settings: Improper automatic control system settings on the production line may result in parameters such as temperature and pressure not reaching their optimal state.
4. Cooling system issues
Insufficient cooling: During the blown film process, if the cooling system fails to work effectively, it will result in insufficient surface smoothness and toughness of the film, thereby affecting the quality of the product.
Insufficient water flow: Insufficient cooling water flow may cause the cooling speed of the film to be too slow, affecting the forming effect of the film.
5. Airflow and stretching issues
Unstable airflow: The stability of airflow is crucial during the film blowing process. Fluctuations in airflow can lead to uneven membrane thickness or the generation of bubbles.
Uneven stretching: If there is an uneven phenomenon during the stretching process of the film, it may lead to the strength and toughness of the film not meeting the standards.
Suggested solution:
Regular maintenance: Regularly inspect and maintain equipment, including heating, extrusion, and cooling systems.
Raw material management: Ensure the humidity and uniformity of raw materials, and avoid using damp or unevenly mixed raw materials.
Training operators: Strengthen the training of operators to ensure they are familiar with the equipment operation process and emergency response measures.
Set up monitoring system: Use an automatic monitoring system to track parameters in real-time during the production process, adjust them in a timely manner to ensure optimal production conditions are achieved.
By making these preparations and maintenance, it is possible to effectively reduce the problems that may be encountered when starting the stone paper blown film paper machine, improve production efficiency and product quality.

Raw material humidity: The main components of stone paper are calcium carbonate and resin. If the humidity of the raw material is high, it may cause problems during the film formation process, affecting the quality of the film.
Uneven mixing of raw materials: Improper proportioning or uneven mixing of raw materials for stone paper may lead to unstable properties of the molten material, thereby affecting the quality of the final film.
2. Equipment issues
Heating failure: If the heating device does not work properly before starting up, it may cause the raw materials to fail to reach the required melting temperature, affecting the extrusion process.
Blockage of extruder: If the equipment is not cleaned thoroughly or there are impurities in the raw materials after the last production, it may cause blockage of the extruder and affect the production process.
Mold malfunction: If the mold part is not installed correctly or damaged, it can cause uneven film thickness or defects.
3. Operational issues
Insufficient training for operators: If operators are not familiar with the operation process of the equipment, they may make operational errors, resulting in the equipment not being able to start normally.
Improper control system settings: Improper automatic control system settings on the production line may result in parameters such as temperature and pressure not reaching their optimal state.
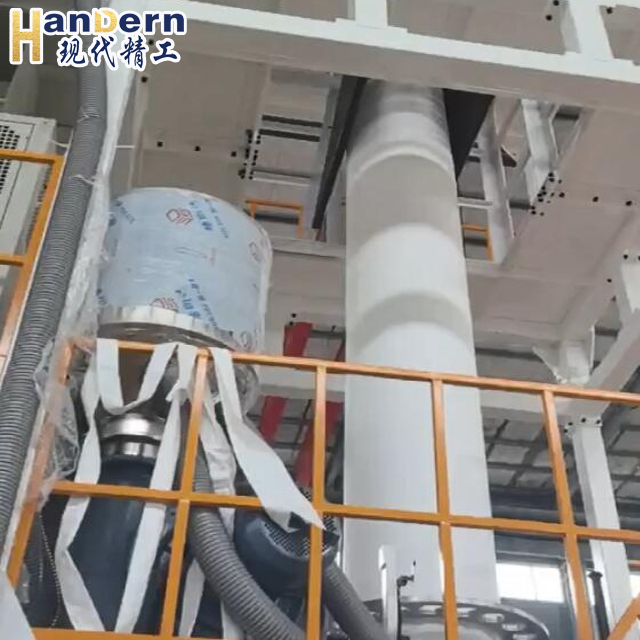
Insufficient cooling: During the blown film process, if the cooling system fails to work effectively, it will result in insufficient surface smoothness and toughness of the film, thereby affecting the quality of the product.
Insufficient water flow: Insufficient cooling water flow may cause the cooling speed of the film to be too slow, affecting the forming effect of the film.
5. Airflow and stretching issues
Unstable airflow: The stability of airflow is crucial during the film blowing process. Fluctuations in airflow can lead to uneven membrane thickness or the generation of bubbles.
Uneven stretching: If there is an uneven phenomenon during the stretching process of the film, it may lead to the strength and toughness of the film not meeting the standards.
Suggested solution:
Regular maintenance: Regularly inspect and maintain equipment, including heating, extrusion, and cooling systems.
Raw material management: Ensure the humidity and uniformity of raw materials, and avoid using damp or unevenly mixed raw materials.
Training operators: Strengthen the training of operators to ensure they are familiar with the equipment operation process and emergency response measures.
Set up monitoring system: Use an automatic monitoring system to track parameters in real-time during the production process, adjust them in a timely manner to ensure optimal production conditions are achieved.
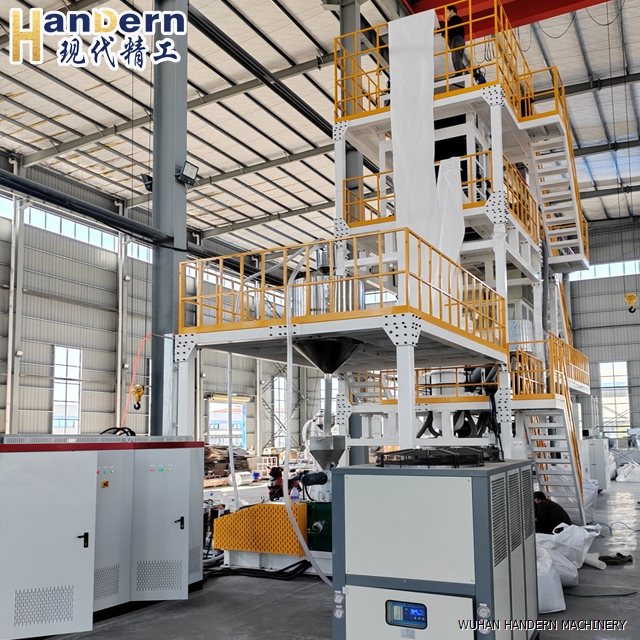
Author:admin