Why do the boards produced by the plastic hollow board production line have cracks
DATE:2024/11/14 11:08:34 / READ: / SOURCE:This station
If cracks occur during the production process of plastic hollow board production line, it usually seriously affects the product quality and performance. The occurrence of cracks is often related to multiple factors, and the following are the main reasons that may cause cracks in plastic hollow boards:
1. Quality issues with raw materials
Raw material moisture content: If the moisture content of polypropylene (PP) or other raw materials used is too high, the moisture is easily dissociated during high-temperature melting, forming bubbles or cracks, thereby affecting the overall structure of the board.
Additive issue: Some additives may have a negative impact on the performance of materials, and excessive use or incompatible additives may also cause cracks in materials during processing.
2. Extrusion process parameters
Temperature setting: Setting the temperature too low during the extrusion process may result in insufficient melting of the material, forming hard small particles that may cause cracks during the forming process. In addition, excessive temperature may also lead to polymer degradation, poor flowability, and cracking.
Extrusion speed: If the extrusion speed is too fast and the material stays in the mold for too short a time, it may not be fully cured or stretched, which can also cause cracks on the surface of the sheet.
3. Improper cooling process
Cooling rate: During the cooling process, rapid or uneven temperature changes can lead to internal stress concentration, resulting in the formation of cracks. Especially during instantaneous cooling, it is easy to cause brittle fracture of materials.
Cooling medium: The flow rate, pressure, and water temperature of the cooling water used may affect the cooling effect, thereby affecting the internal stress and stability of the board.
4. Mechanical equipment status
Equipment wear: The degree of wear of screws, molds, and other equipment can affect the extrusion quality of materials. If the wear is severe, it may cause uneven melting of the material, resulting in cracks in the finished product.
Feeding system: If the feeding system is unstable and causes intermittent material supply, it may result in uneven stress during the melting process, leading to cracks.
5. External environmental influences
Production environment: Temperature and humidity in the workshop, improper environmental conditions may have an impact on the properties of plastics. If the temperature is too low, it may affect the toughness of the material, leading to cracks during the molding process.
6. Post molding processing
Cutting and handling: In the subsequent process, collisions, pressures, etc. during cutting and transportation may cause stress on the sheet, leading to the occurrence of cracks.
Storage method: Improper storage method may cause cracks in the board under stress, such as stacking too high or unevenly.
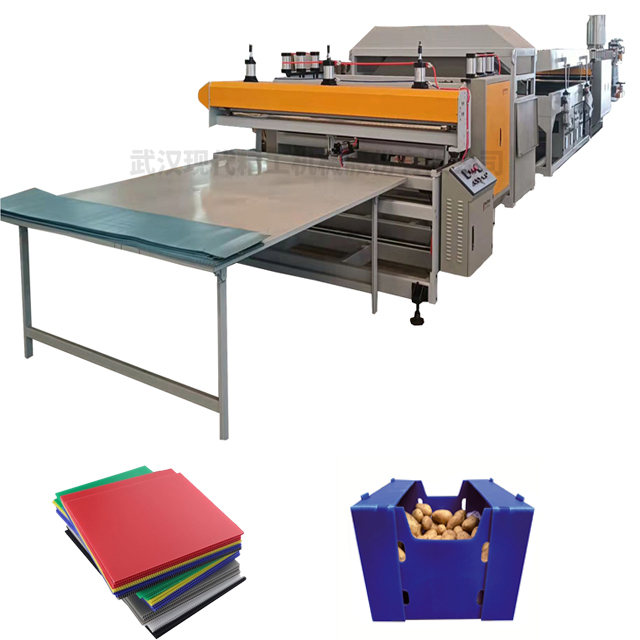
Raw material moisture content: If the moisture content of polypropylene (PP) or other raw materials used is too high, the moisture is easily dissociated during high-temperature melting, forming bubbles or cracks, thereby affecting the overall structure of the board.
Additive issue: Some additives may have a negative impact on the performance of materials, and excessive use or incompatible additives may also cause cracks in materials during processing.
2. Extrusion process parameters
Temperature setting: Setting the temperature too low during the extrusion process may result in insufficient melting of the material, forming hard small particles that may cause cracks during the forming process. In addition, excessive temperature may also lead to polymer degradation, poor flowability, and cracking.
Extrusion speed: If the extrusion speed is too fast and the material stays in the mold for too short a time, it may not be fully cured or stretched, which can also cause cracks on the surface of the sheet.
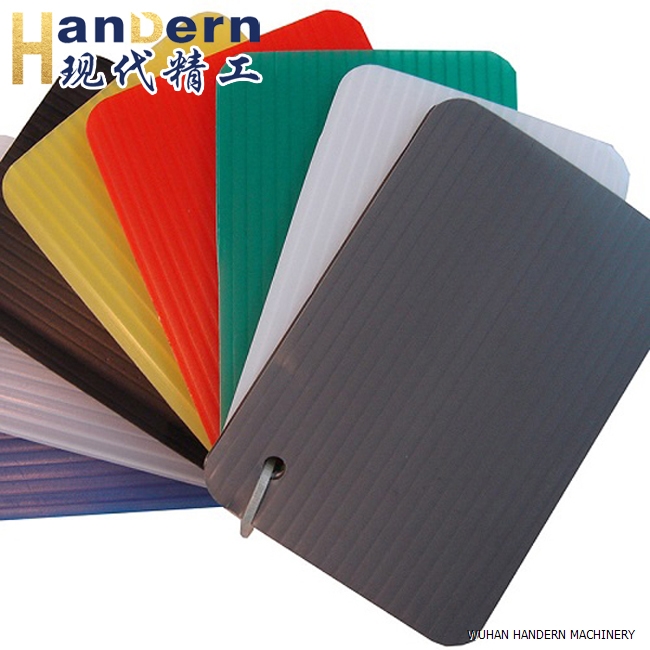
Cooling rate: During the cooling process, rapid or uneven temperature changes can lead to internal stress concentration, resulting in the formation of cracks. Especially during instantaneous cooling, it is easy to cause brittle fracture of materials.
Cooling medium: The flow rate, pressure, and water temperature of the cooling water used may affect the cooling effect, thereby affecting the internal stress and stability of the board.
4. Mechanical equipment status
Equipment wear: The degree of wear of screws, molds, and other equipment can affect the extrusion quality of materials. If the wear is severe, it may cause uneven melting of the material, resulting in cracks in the finished product.
Feeding system: If the feeding system is unstable and causes intermittent material supply, it may result in uneven stress during the melting process, leading to cracks.
5. External environmental influences
Production environment: Temperature and humidity in the workshop, improper environmental conditions may have an impact on the properties of plastics. If the temperature is too low, it may affect the toughness of the material, leading to cracks during the molding process.
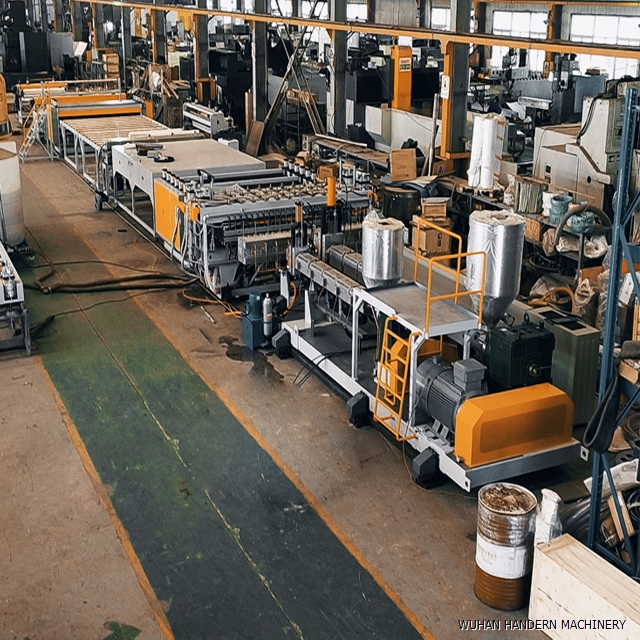
Cutting and handling: In the subsequent process, collisions, pressures, etc. during cutting and transportation may cause stress on the sheet, leading to the occurrence of cracks.
Storage method: Improper storage method may cause cracks in the board under stress, such as stacking too high or unevenly.
Author:admin