What are the common problems in the operation of a biaxially oriented film production line
DATE:2024/10/28 10:39:34 / READ: / SOURCE:This station
The production line of biaxially oriented films (BOPP or BOPET) may encounter various common problems during operation, which not only affect production efficiency but may also have a significant impact on the quality of the final product. Here are some common problems, their possible causes, and solutions:
1. Material issues
Problem: Unstable quality of raw materials may result in uneven film or the formation of bubbles.
Reason: The moisture and impurity content of the raw materials is too high, or the variety of the raw materials does not match.
Solution:
Select high-quality raw materials and ensure that they meet production standards.
Regularly check the storage conditions of raw materials to ensure dryness and cleanliness.
2. Heating and temperature control issues
Problem: The temperature of the film is uneven during heating, resulting in uneven stretching or wrinkling of the film.
Reason: Heating device malfunction or inaccurate temperature control system.
Solution:
Regularly calibrate the temperature sensor and check the working status of the heater.
Problem: Uneven stretching ratio leads to inconsistent mechanical properties of the film, such as decreased strength and transparency.
Reason: Improper adjustment of the tensioner or malfunction of the drive system.
Solution:
Regularly calibrate the stretching equipment to ensure that the stretching ratio meets the design requirements.
Monitor the stretching speed to ensure its uniformity.
4. Equipment malfunction
Problem: Malfunction of the stretching machine or extruder, such as material blockage or vibration.
Reason: Equipment wear and tear or improper maintenance caused by long-term use.
Solution:
Regularly maintain and upkeep mechanical equipment.
Establish a regular inspection and maintenance system for equipment, and promptly replace worn parts.
5. Product defects
Problem: Bubbles, wrinkles, or uneven surfaces appear on the finished film.
Reason: Cooling system malfunction, uneven material flow.
Solution:
Regularly inspect the cooling system to ensure its proper functioning.
Ensure uniform air flow in the thin film cooling channel to prevent local temperatures from being too high or too low.
6. Cutting and winding issues
Problem: The product may experience misalignment or unclean cutting during the cutting or winding process.
Reason: Wear of cutting blade or improper setting of winding device.
Solution:
Regularly inspect and replace cutting blades to ensure their sharpness.
Problem: Excessive humidity or temperature can affect the quality of the film.
Reason: Poor control of workshop environment.
Solution:
Monitor the temperature and humidity in the production workshop, and use air conditioning or dehumidifiers to maintain stable environmental conditions.
During the production process, try to avoid exposing the film to high humidity or high temperature environments.
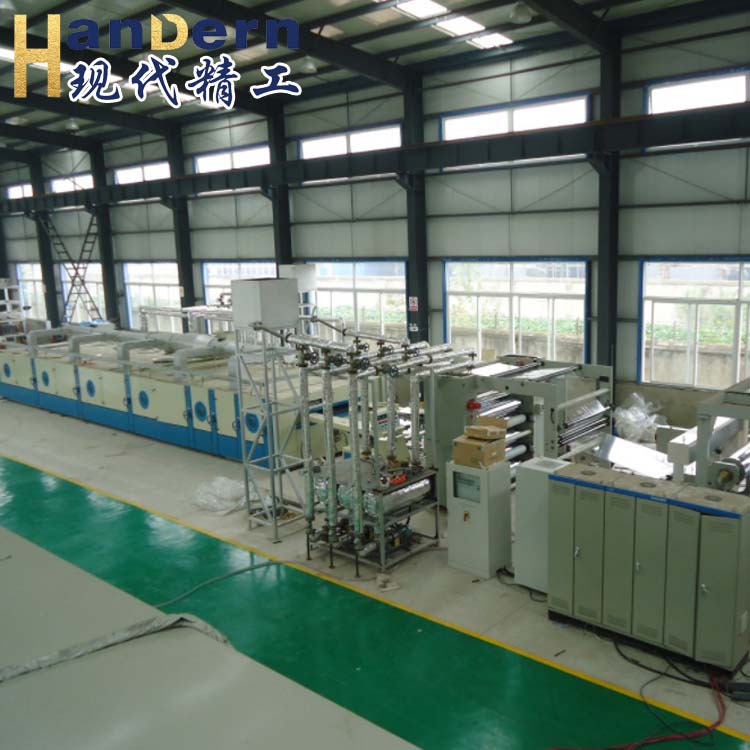
Problem: Unstable quality of raw materials may result in uneven film or the formation of bubbles.
Reason: The moisture and impurity content of the raw materials is too high, or the variety of the raw materials does not match.
Solution:
Select high-quality raw materials and ensure that they meet production standards.
Regularly check the storage conditions of raw materials to ensure dryness and cleanliness.
2. Heating and temperature control issues
Problem: The temperature of the film is uneven during heating, resulting in uneven stretching or wrinkling of the film.
Reason: Heating device malfunction or inaccurate temperature control system.
Solution:
Regularly calibrate the temperature sensor and check the working status of the heater.
Clean the heating channel to ensure that there are no foreign objects obstructing the heating effect.
Problem: Uneven stretching ratio leads to inconsistent mechanical properties of the film, such as decreased strength and transparency.
Reason: Improper adjustment of the tensioner or malfunction of the drive system.
Solution:
Regularly calibrate the stretching equipment to ensure that the stretching ratio meets the design requirements.
Monitor the stretching speed to ensure its uniformity.
4. Equipment malfunction
Problem: Malfunction of the stretching machine or extruder, such as material blockage or vibration.
Reason: Equipment wear and tear or improper maintenance caused by long-term use.
Solution:
Regularly maintain and upkeep mechanical equipment.
Establish a regular inspection and maintenance system for equipment, and promptly replace worn parts.
5. Product defects
Problem: Bubbles, wrinkles, or uneven surfaces appear on the finished film.
Reason: Cooling system malfunction, uneven material flow.
Solution:
Regularly inspect the cooling system to ensure its proper functioning.
Ensure uniform air flow in the thin film cooling channel to prevent local temperatures from being too high or too low.
6. Cutting and winding issues
Problem: The product may experience misalignment or unclean cutting during the cutting or winding process.
Reason: Wear of cutting blade or improper setting of winding device.
Solution:
Regularly inspect and replace cutting blades to ensure their sharpness.
Adjust the pressure of the winding equipment to ensure even winding of the film.
Problem: Excessive humidity or temperature can affect the quality of the film.
Reason: Poor control of workshop environment.
Solution:
Monitor the temperature and humidity in the production workshop, and use air conditioning or dehumidifiers to maintain stable environmental conditions.
During the production process, try to avoid exposing the film to high humidity or high temperature environments.
Author:admin