Detailed introduction of PEEK film casting production equipment
DATE:2024/9/10 10:55:35 / READ: / SOURCE:This station
Polyether ether ketone (PEEK) film is a linear aromatic polymer film with a series of outstanding characteristics, such as excellent mechanical properties, heat resistance, flame retardancy, wear resistance, corrosion resistance, hydrolysis resistance, peel resistance, and biocompatibility. Because PEEK film has such excellent properties, it has also become the most extensively studied and widely commercialized representative in the polyaryletherketone (PAEK) family.
1、 Basic characteristics of PEEK film
At present, the production method of PEEK film mainly adopts extrusion casting method. Due to the certain speed of PEEK film casting equipment, the film will undergo a certain amount of stretching in the longitudinal direction. In addition, the temperature and speed of PEEK film casting equipment directly affect the structure, morphology, and thickness of the film. When the film thickness is the same, the higher the crystallinity, the lower the transmittance. The haze of a film can also reflect its color state. The higher the crystallinity, the higher the haze value. When the crystallinity is below 5%, the film exhibits high transparency.
2、 Process requirements for PEEK film casting equipment
To achieve smooth production of PEEK film, certain requirements will be placed on the corresponding production equipment. Currently, the required screw parameters for PEEK film casting equipment are aspect ratio L/D: 24:1-30:1, feed section:>8D, compression ratio CR: 2-3. The recommended screw type must be a cylindrical heating ring that can maintain 400 ℃. It is recommended to use at least four independent heating zones, each with independent thermocouples and proportional integral derivative (PID) controllers, for precise temperature control, with temperature controlled within ± 2 ℃.
Additionally, it should be noted that the size of the extruder should match the equipment output, and ideally, the dwell time should be less than 30 minutes. For example, when the screw speed is low (<10rpm), the extrusion process will lead to longer residence time and increase the probability of gel degradation. All inner surfaces should have no "dead corners" and be cleaned and polished before extrusion begins; The porous plate of the machine head helps to generate back pressure in the screw and stop the rotation of the melt. The hole size should be proportional to the extruder size and designed to eliminate dead corners as much as possible. The hole should be chamfered to enhance fluidity.
Usually, the filter group is placed in front of the filter to remove any residual impurities from the material. If the filter screen is too fine, it will generate excessive shear and pressure drop in the melt. Dead corners/low flow rates can lead to local degradation, resulting in material discoloration or black spots in the melt. Therefore, the flow rate through the machine head, mold head, and mold should have a transition in flow pattern, and the cross-sectional changes should be gradual. The joints must be aligned without gaps. The system can be simulated to ensure that there are no low flow areas.
It is recommended to use separately controlled heaters for each part (head, flange, die) and apply insulation materials as much as possible for thermal insulation. Slit molds are commonly used for processing natural PEEK sheets, and controlling the temperature of the mold lip is crucial for good surface smoothness and dimensional control. Thin films (<500 μ m) can be produced in semi crystalline or amorphous form by controlling the temperature of the rollers. If the temperature of the drum is lower than Tg, an amorphous transparent film will be produced, while if the temperature is higher than 170 ℃, an opaque semi crystalline film will be produced. Thicker films can crystallize under their own retained heat.
3、 Application scenarios of PEEK film
PEEK films are mainly divided into two categories, namely high crystalline PEEK films and low crystalline PEEK films. The surface morphology of films can be divided into three different effects: glossy/glossy, glossy/matte, and matte/matte. Special types include carbon fiber reinforced and mineral reinforced films to meet the application requirements of different customers on different products. Its application areas are mainly distributed in planar transducers, compression drive edge suspensions and high-end speakers, smartphones, laptops/tablets, car speakers, televisions/soundbars, smart speakers, headphones and true wireless earplugs.
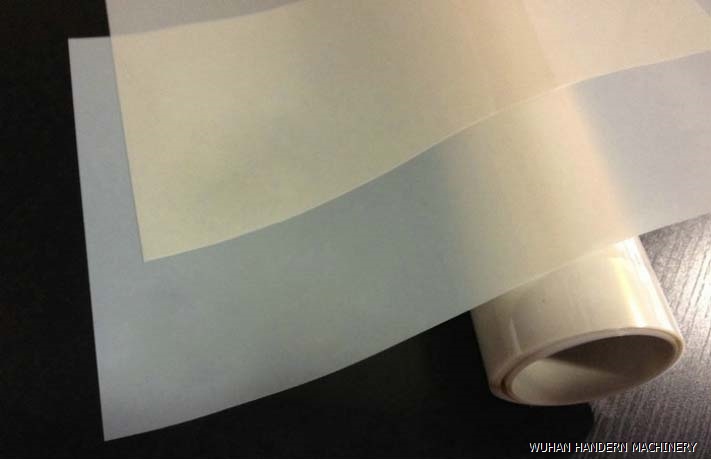
At present, the production method of PEEK film mainly adopts extrusion casting method. Due to the certain speed of PEEK film casting equipment, the film will undergo a certain amount of stretching in the longitudinal direction. In addition, the temperature and speed of PEEK film casting equipment directly affect the structure, morphology, and thickness of the film. When the film thickness is the same, the higher the crystallinity, the lower the transmittance. The haze of a film can also reflect its color state. The higher the crystallinity, the higher the haze value. When the crystallinity is below 5%, the film exhibits high transparency.
2、 Process requirements for PEEK film casting equipment
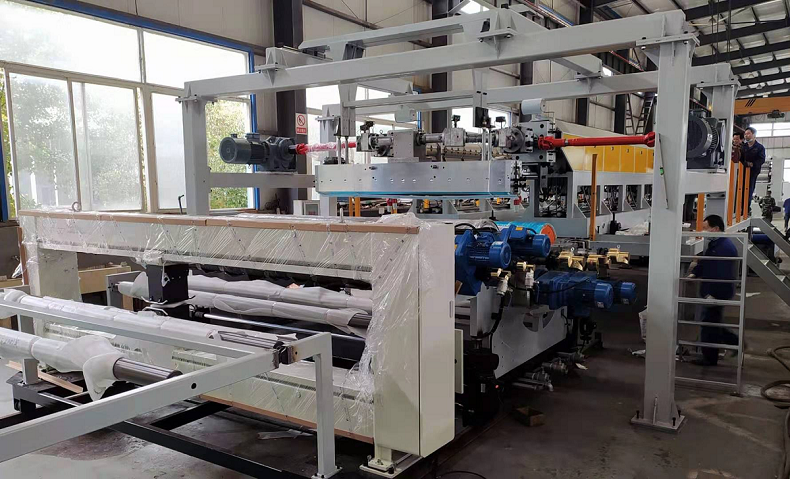
Additionally, it should be noted that the size of the extruder should match the equipment output, and ideally, the dwell time should be less than 30 minutes. For example, when the screw speed is low (<10rpm), the extrusion process will lead to longer residence time and increase the probability of gel degradation. All inner surfaces should have no "dead corners" and be cleaned and polished before extrusion begins; The porous plate of the machine head helps to generate back pressure in the screw and stop the rotation of the melt. The hole size should be proportional to the extruder size and designed to eliminate dead corners as much as possible. The hole should be chamfered to enhance fluidity.
Usually, the filter group is placed in front of the filter to remove any residual impurities from the material. If the filter screen is too fine, it will generate excessive shear and pressure drop in the melt. Dead corners/low flow rates can lead to local degradation, resulting in material discoloration or black spots in the melt. Therefore, the flow rate through the machine head, mold head, and mold should have a transition in flow pattern, and the cross-sectional changes should be gradual. The joints must be aligned without gaps. The system can be simulated to ensure that there are no low flow areas.
It is recommended to use separately controlled heaters for each part (head, flange, die) and apply insulation materials as much as possible for thermal insulation. Slit molds are commonly used for processing natural PEEK sheets, and controlling the temperature of the mold lip is crucial for good surface smoothness and dimensional control. Thin films (<500 μ m) can be produced in semi crystalline or amorphous form by controlling the temperature of the rollers. If the temperature of the drum is lower than Tg, an amorphous transparent film will be produced, while if the temperature is higher than 170 ℃, an opaque semi crystalline film will be produced. Thicker films can crystallize under their own retained heat.
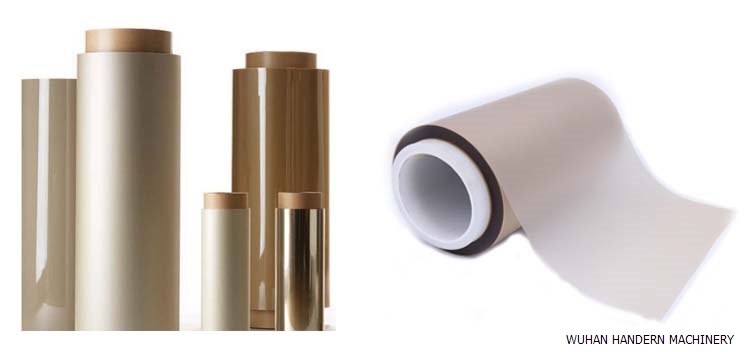
PEEK films are mainly divided into two categories, namely high crystalline PEEK films and low crystalline PEEK films. The surface morphology of films can be divided into three different effects: glossy/glossy, glossy/matte, and matte/matte. Special types include carbon fiber reinforced and mineral reinforced films to meet the application requirements of different customers on different products. Its application areas are mainly distributed in planar transducers, compression drive edge suspensions and high-end speakers, smartphones, laptops/tablets, car speakers, televisions/soundbars, smart speakers, headphones and true wireless earplugs.
Author:admin