What should I do if there is an emergency stop fault in the hollow board production line
DATE:2024/8/26 14:59:35 / READ: / SOURCE:This station
During the operation of the hollow board production line, emergency stop faults may occur due to operational errors, equipment failures, or other factors. The impact caused by such faults is enormous, such as production stoppage, equipment damage, safety issues, etc. Therefore, it is particularly important to prevent the occurrence of such faults and promptly and effectively solve them after they occur. So, what should we do in the face of these? Below, the editor will teach you how to deal with sudden shutdown faults in the hollow board production line.
1. Preliminary inspection and confirmation
When an emergency stop occurs on the production line, conduct a preliminary inspection of the production line. Confirm whether the emergency stop was caused by equipment malfunction, material issues, or operational errors. Some common causes of malfunctions may include power failure, overheating, transmission system problems, sensor failures, etc. The operator should quickly check the equipment display screen or alarm device to understand the cause of the malfunction.
2. Safety first, power outage and protection
After confirming the fault, it is necessary to ensure that all equipment is in a safe state as soon as possible. Usually, power can be cut off by pressing the emergency stop button on the control panel or manually turning off the power. This step is very important to prevent further damage or safety accidents from occurring. At the same time, ensure that there are no personnel in danger on the production site and evacuate unrelated personnel in accordance with safety regulations.
3. Troubleshooting
After power failure, conduct a detailed inspection. During the inspection process, focus on the following aspects:
Electrical system: Check whether the power cord is damaged, whether the electrical components are working properly, and whether there is a short circuit or overload phenomenon.
Mechanical system: Check whether the transmission system is operating normally, whether there are foreign objects stuck in the equipment, and whether the transmission components such as gears and belts are worn or broken.
Control system: Check if sensors, switches, and other control components are working properly and if there are any malfunctions.
4. Seek professional support
If the operator is unable to solve the problem after on-site troubleshooting, they should contact the manufacturer or professional maintenance personnel of the hollow board production line as soon as possible for in-depth maintenance. Provide detailed fault conditions and inspection results so that professionals can quickly assess and develop corresponding maintenance plans.
5. Recording and feedback
After troubleshooting, the fault situation, troubleshooting, and repair process should be recorded in a timely manner. These pieces of information not only facilitate the rapid handling of similar faults in the future, but also provide important references for equipment maintenance and upkeep. At the same time, report the fault situation to the management in order to optimize the production process and safety plan.
6. Device restart and monitoring
After the fault is repaired, restart the device according to the manufacturer's operating procedures. At the same time, in the initial stage of resuming production, monitoring of equipment operation status should be strengthened to ensure that everything is normal before returning to normal production pace, reducing the risk of sudden stops again.
7. Preventive measures
In order to reduce the probability of emergency shutdown failures in the hollow board production line, it is recommended to regularly maintain the equipment, replace worn parts in a timely manner, maintain a clean and tidy production environment, and strengthen training to improve the operational skills of operators to cope with unexpected situations.
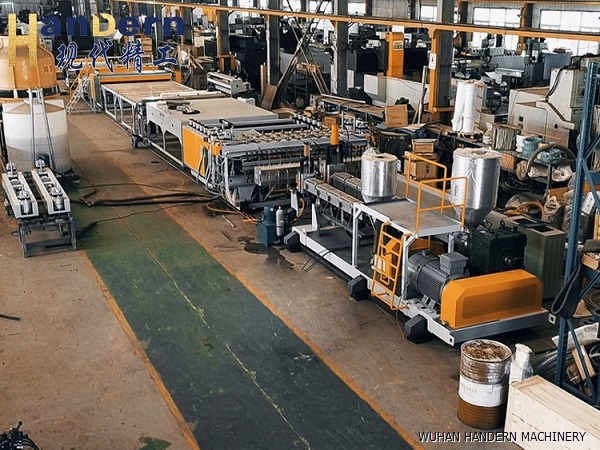
When an emergency stop occurs on the production line, conduct a preliminary inspection of the production line. Confirm whether the emergency stop was caused by equipment malfunction, material issues, or operational errors. Some common causes of malfunctions may include power failure, overheating, transmission system problems, sensor failures, etc. The operator should quickly check the equipment display screen or alarm device to understand the cause of the malfunction.
After confirming the fault, it is necessary to ensure that all equipment is in a safe state as soon as possible. Usually, power can be cut off by pressing the emergency stop button on the control panel or manually turning off the power. This step is very important to prevent further damage or safety accidents from occurring. At the same time, ensure that there are no personnel in danger on the production site and evacuate unrelated personnel in accordance with safety regulations.
3. Troubleshooting
After power failure, conduct a detailed inspection. During the inspection process, focus on the following aspects:
Electrical system: Check whether the power cord is damaged, whether the electrical components are working properly, and whether there is a short circuit or overload phenomenon.
Mechanical system: Check whether the transmission system is operating normally, whether there are foreign objects stuck in the equipment, and whether the transmission components such as gears and belts are worn or broken.
Control system: Check if sensors, switches, and other control components are working properly and if there are any malfunctions.
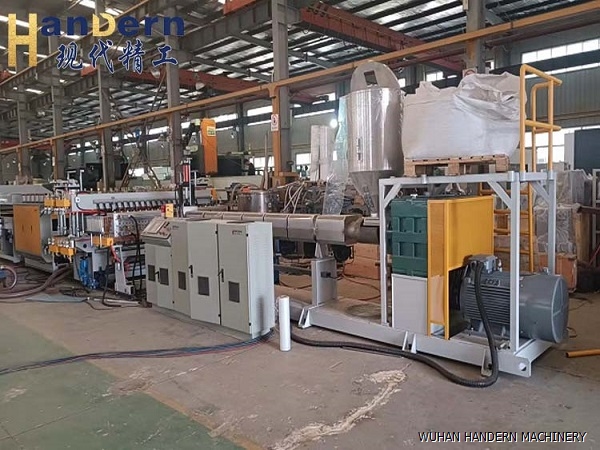
If the operator is unable to solve the problem after on-site troubleshooting, they should contact the manufacturer or professional maintenance personnel of the hollow board production line as soon as possible for in-depth maintenance. Provide detailed fault conditions and inspection results so that professionals can quickly assess and develop corresponding maintenance plans.
5. Recording and feedback
After troubleshooting, the fault situation, troubleshooting, and repair process should be recorded in a timely manner. These pieces of information not only facilitate the rapid handling of similar faults in the future, but also provide important references for equipment maintenance and upkeep. At the same time, report the fault situation to the management in order to optimize the production process and safety plan.
6. Device restart and monitoring
After the fault is repaired, restart the device according to the manufacturer's operating procedures. At the same time, in the initial stage of resuming production, monitoring of equipment operation status should be strengthened to ensure that everything is normal before returning to normal production pace, reducing the risk of sudden stops again.
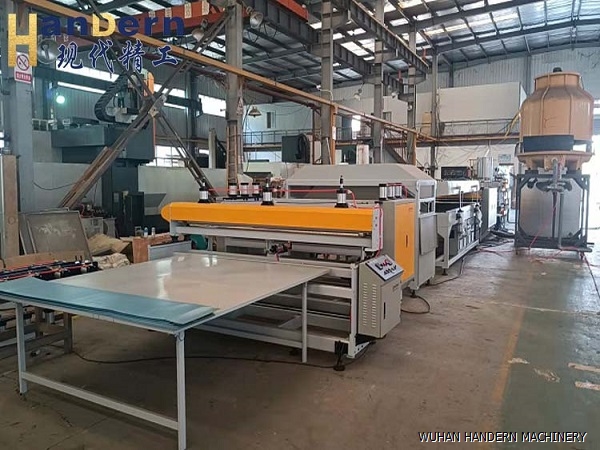
In order to reduce the probability of emergency shutdown failures in the hollow board production line, it is recommended to regularly maintain the equipment, replace worn parts in a timely manner, maintain a clean and tidy production environment, and strengthen training to improve the operational skills of operators to cope with unexpected situations.
Author:admin