Interpreting the advantages and processes of hollow board production lines
DATE:2023/4/18 14:51:09 / READ: / SOURCE:This station
Before using hollow boards, cardboard had always been used in the industry. The production speed of cardboard was fast, the production volume was large, and the later processing was convenient. However, the production cost of cardboard was high, and the usage conditions were limited. This made it urgent for people to replace cardboard with another material, resulting in the current hollow board.
Hollow board is a type of hollow board made of PP (polypropylene) or PE (polyethylene) materials, which is usually used to replace traditional cardboard or wooden boards. Due to its lightweight, sturdy, water resistant, corrosion-resistant, seismic resistant, and environmentally friendly properties, hollow panels are widely used in packaging, transportation, construction, advertising, and other fields.
Compared to cardboard, hollow boards have higher strength, are less prone to deformation, and have a longer service life. In addition, the surface of the hollow board is smooth and easy to print, which can achieve better advertising effects. At the same time, hollow boards can better prevent moisture, water, and fire.
Overall, hollow boards can effectively replace traditional cardboard and become more environmentally friendly, economical, and practical packaging and building materials.
Modern Seiko has been engaged in the research and development, production, and sales of hollow board production lines for 20 years. If you have any questions about hollow boards or hollow board production lines, you can feel free to consult us at any time. Today, the editor will briefly introduce the production process of hollow plates to everyone. In simple terms, the production process of hollow plates consists of three steps: material preparation, extrusion molding, cutting, and more details. The specific content of these three steps is as follows:
1. Material preparation: Add polypropylene (PP) or polyethylene (PE) particles to the extruder, add pigments and other additives, and mix evenly.
2. Extrusion: Melted plastic is extruded into a plate shape through an extruder, and then processed by a molding machine to form a hollow plate. The pore structure of the hollow board can be made by selecting different molds according to needs.
3. Cutting: Cut the hollow board according to the required length and width. The cutting method can be manual or mechanical to ensure the required accuracy.
After completing the above three steps, we also need to conduct quality inspection on the finished product to check whether its appearance quality, dimensional accuracy, and physical performance indicators meet the requirements.
The process of the hollow board production line is relatively simple, with high production efficiency and stable product quality, widely used in various fields.
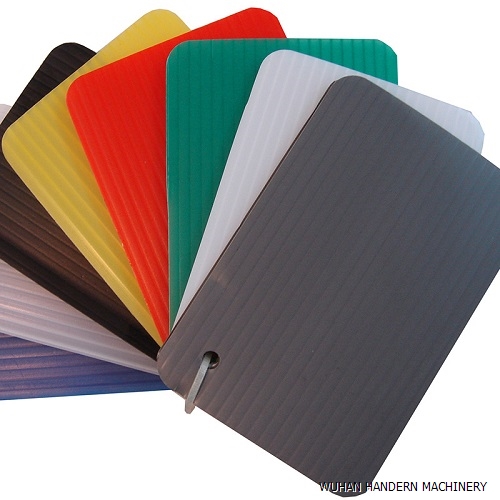
Compared to cardboard, hollow boards have higher strength, are less prone to deformation, and have a longer service life. In addition, the surface of the hollow board is smooth and easy to print, which can achieve better advertising effects. At the same time, hollow boards can better prevent moisture, water, and fire.
Overall, hollow boards can effectively replace traditional cardboard and become more environmentally friendly, economical, and practical packaging and building materials.
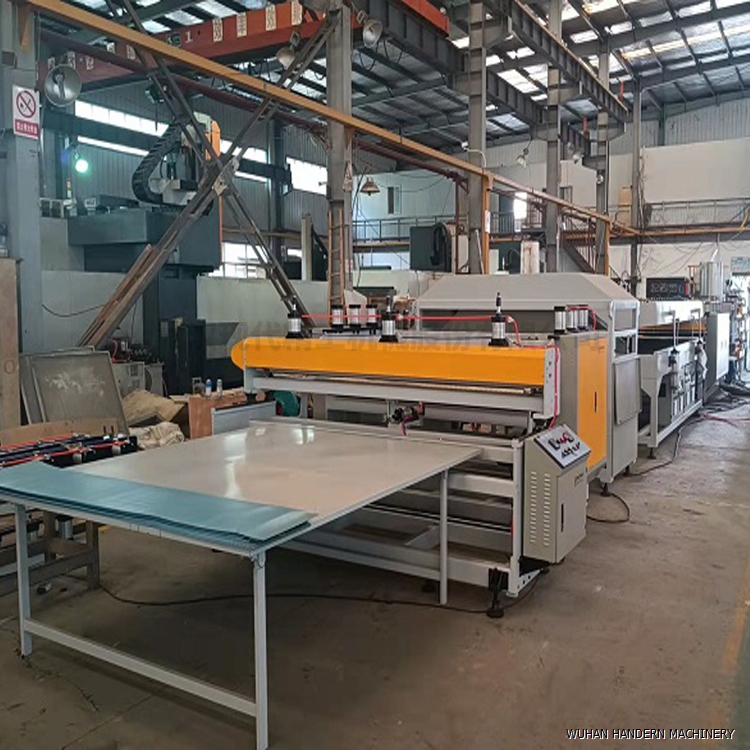
1. Material preparation: Add polypropylene (PP) or polyethylene (PE) particles to the extruder, add pigments and other additives, and mix evenly.
2. Extrusion: Melted plastic is extruded into a plate shape through an extruder, and then processed by a molding machine to form a hollow plate. The pore structure of the hollow board can be made by selecting different molds according to needs.
3. Cutting: Cut the hollow board according to the required length and width. The cutting method can be manual or mechanical to ensure the required accuracy.
After completing the above three steps, we also need to conduct quality inspection on the finished product to check whether its appearance quality, dimensional accuracy, and physical performance indicators meet the requirements.
The process of the hollow board production line is relatively simple, with high production efficiency and stable product quality, widely used in various fields.
Author:admin